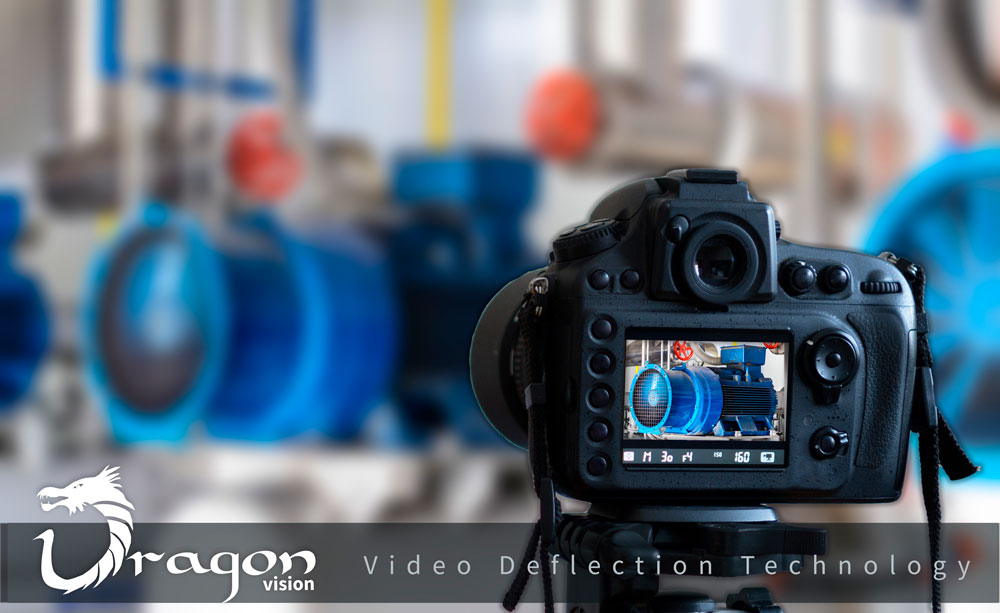
The Looking Glass Technique – See the Invisible
Incredible as it may seem, the vibration (or at least a large part of it) can be detected through video recording with incredible resolution. Saving a huge number of hours in studies that before were time consuming if not impossible to do.
Inspired by the EC-135 Airborne Command and Control Aircraft that served as the United Nations strategic airborne launch control and command center during the cold war Optical Vibration has created the Looking Glass Technique within DragonVision® to differentiate it from common techniques.
So, what is the Vibration Tracking? And better yet, what is it for?
What is the Looking Glass Technique?
The Looking Glass Technique is the Optical Vibration method used to obtain Meaningful Vibration signals from a video recording combined with a unique and trusted calibration method that utilizes a traditional accelerometer signal. It is a vibration analysis method that uses our unique micro motion tracking algorithm in video files. In fact, it is used today to detect and measure vibrations of thousands of points simultaneously with only one video recording.
The results of this type of vibration analysis depend on the quality of the recording. Likewise, the maximum frequency visible in the spectra is related to the number of frames per second that have been taken.
Learn more about DragonVision® – Video Deflection Technology.
How can Looking Glass Technique help me?
Video Vibration Tracking allows users to measure thousands of points at the same time which, otherwise, would be either impossible to measure or they would consume a lot of time with conventional methods. In this way, it gives you the possibility to analyze structures, movement, deflection and phase much more precisely, and with very little effort. At the same time, this technique allows users to export amplified vibration simulations that are very easy to interpret even for people who are not experts in vibrational analysis.
How does the Looking Glass technique work?
The smallest movement that this method can detect is much smaller than the pixel size of a conventional camera. So how does it work?
The principle of this method is based on the fact that, in a conventional camera, before an object moves from one pixel to another, it creates a small color change in the next pixel. In fact the color from both pixels change progressively until the object occupies entirely the next pixel sensor.
This method measures the changes in angularity and changes in the amount of color from each pixels (In fact from an entire area of pixels). First, the software identifies color patterns within small user defined areas. These patterns must have changes in angularity and color differences in order to distinguish it from the rest of the patterns. The target areas are found automatically by the software and the user can only modify some quality parameters and surface.
Second, for each video frame, the software will identify the average color changes on the targeted points and its corresponding area. Thus, being able to track small changes in each frame with great accuracy.
Finally, all that information obtained is translated into vibration signals like an FFT, phase, or time wave form for analytical purposes.
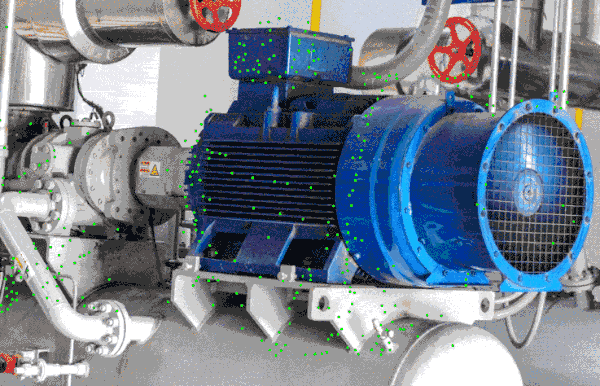
Reliability in Amplitude
To obtain reliable vibration values, it is essential to have a calibration system. All cameras have different types of lenses, as well as resolutions, not to mention that the Zoom used and the distance at which the video is taken can change the appreciation of the movement.
Therefore, the system needs a comparative calibration to achieve reliability. The best method to calibrate these signals is using an accelerometer.
There are 2 comparative methods used to calibrate these type of signals:
By RMS value: this method requires a single point on the machine to be measured with a conventional vibrometer. The software will then calibrate the movement according to the RMS value of that point.
By Cross Channel: this method is the most accurate and requires a complete recording of the vibration signal for the software to process it in the form of a spectrum (FFT). Using this method the software will be able to calibrate each frequency individually eliminating false frequencies that could be generated by the Aliasing effect.
WiSER 3x
Wireless Triaxial Accelerometer-
-
Triaxial Accelerometer
-
Full bandwidth 10kHz
-
Long distance range up to 20m
-
Stainless steel housing
-
Operation temperature up to 185ºF (80ºC)
-
Ideal for Real Life ODS & Route Based Data Collection
What failures can I diagnose with the Looking Glass Technique?
There are many failures that can be detected with this technique. Mainly those related to low frequencies and phase. For example:
- Imbalance
- Misalignment
- Mechanical Looseness
- Bent Shaft
- Eccentricity
- Resonance
- Natural Frequencies (By shock test)
- Electrical Noise
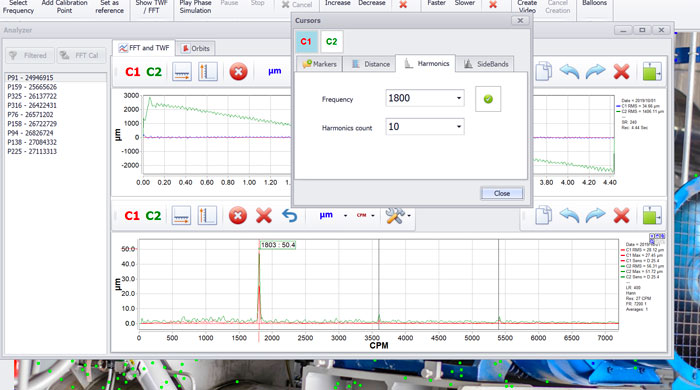
Differential Vibration Analysis
Differential vibration analysis is a study that analyzes the vibration of one area by subtracting the vibrations of another zone. An example is to measure the vibration of an electric motor by subtracting the vibration from its own base (which could be generated by a larger mass or by another motor). This method analyzes the vibration coming exclusively from this motor.
Differential vibration analysis is a very rare type of study due to the difficulty of doing it with current techniques. With the Looking Glass Technique this is very easy because you only need to select a reference area so that these vibrations are automatically subtracted from the rest of the points.
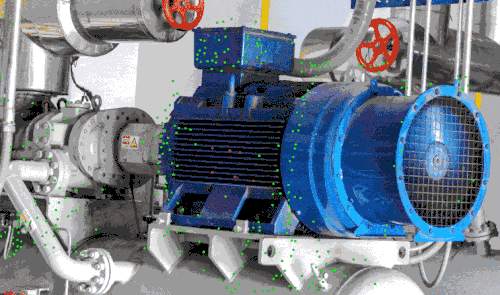
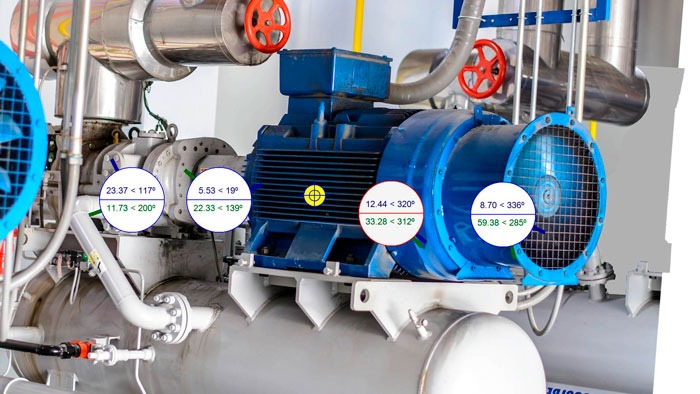
Non-Invasive Vibration Analysis
There are many cases in which the mass of an accelerometer completely changes the behavior of the vibration. This is the case when attempting to gather meaningful data from items with small masses such as a cable, very small motor, radio control airplanes etc.
Looking Glass Technique completely eliminates this problem, since it does not use sensors, the analyzed object will vibrate naturally.
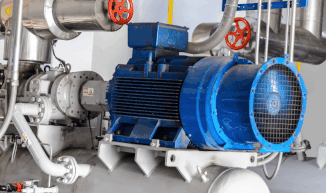
Large scale vibration analysis
Another major limitation of vibration analysis is large scale objects, such as Buildings, Bridges, Large Ships, Airplanes.
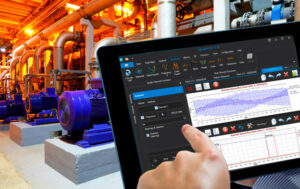
DigivibeMX
The most complete vibration analysis and balancing software in the market.
Whether you balance with your computer or with your smartphone, our free balancing apps have the highest standards.
Limitations of the Vibration Analysis Looking Glass Technique
Looking Glass Technique is an excellent complement for vibration analyzers but not yet a replacement, since it still has some limitations related to maximum frequency and amplitude resolution.
The Maximum Frequency is determined by the number of frames per second taken by the camera (Frame Rate). Thus, the maximum visible frequency will be half of the Frame Rate (and for a reliable amplitude it would be: Frame Rate / 2.56).
Amplitude Resolution will depend on the number of pixels of the camera, as well as the distance from the camera to the object and the zoom used. Obtaining better resolutions when getting closer to the object to be measured.
Aliasing: Another problem with this type of analysis is the impossibility of avoiding the Aliasing effect. Usually common vibration analyzers eliminate this effect using analog filters incorporated within the data acquisition interface. However, in a video this is simply not possible. DragonVision® incorporates a calibration method that relies on a traditional accelerometer, where it analyzes the spectra and eliminates the frequencies caused by the Aliasing effect. Thus, calibrating the signal throughout the entire spectrum, making the reading much more reliable both in frequency and in amplitude. In fact this whole process reduces up to 95% of the floor noise inherent to the camera itself.
For more information on the “Aliasing” effect visit: https://en.wikipedia.org/wiki/Aliasing
Vibration Zone Detection
Virtually immediately. DragonVision® is able to identify the areas with the greatest vibration through a micro-movement detection algorithm. Even isolating and filtering the movements of your own hand while holding the camera.
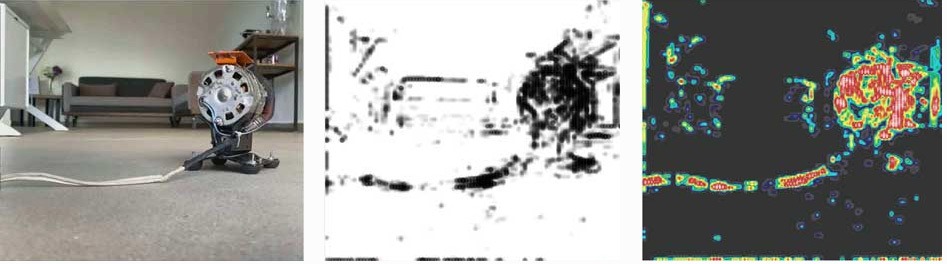
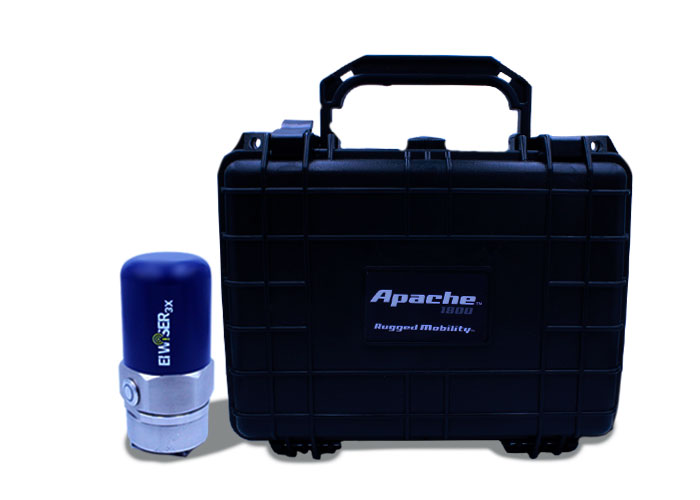
ANTI-ALIASING FILTER
DragonVision® incorporates an anti-aliasing filter that uses cross-channel comparison. In this way, nonexistent frequencies produced by the Aliasing phenomenon due to the low sampling rate of video cameras are eliminated from the FFT.
For more information on the “Aliasing” effect visit: https://en.wikipedia.org/wiki/Aliasing