Is Your Vibration Diagnostic System a Black Box or a White Box? - The Case for Hybrid Rule-Based and Machine Learning Approaches
The Green Doctor Technique
When it comes to vibration diagnostics, do you know how your system makes its decisions? Is it a black box—opaque and mysterious, where the reasoning behind its diagnoses is hidden? Or is it a white box—transparent, with every decision backed by clear, understandable logic? As industries increasingly rely on automated systems for predictive maintenance, understanding how these systems work is crucial not just for trust but also for ensuring the accuracy and reliability of fault detection.
Machine Learning or Rules based Diagnostics?
Another essential aspect of reliable vibration diagnostics is the integration of rule-based analysis with machine learning. While machine learning offers the ability to detect patterns across vast datasets, rule-based systems bring decades of expert knowledge into the equation. These rules, refined over years of study and practice, provide a robust and interpretable foundation for diagnostics.
In this article, we’ll explore how combining these two approaches—leveraging the precision of rule-based analysis with the adaptability of machine learning—can create a powerful, transparent, and trustworthy vibration diagnostic tool.
Understanding Rule-Based Analysis in Vibration Diagnostics and the Green Doctor Technique
What is Rule-Based Analysis?
Rule-based analysis is a diagnostic approach that uses predefined rules, derived from expert knowledge, to interpret vibration data and diagnose faults. Experienced vibration analysts craft these rules, which correspond to specific fault conditions like misalignment, imbalance, bearing defects, or looseness. The rules use input data from vibration sensors to assess the likelihood of these faults.
How Does Rule-Based Analysis Work?
The process begins by collecting data from vibration sensors, typically in the form of time waveform (TWF) and fast Fourier transform (FFT) spectra. Key features such as overall root mean square (RMS) values, 1X amplitude, harmonics, crest factor, and phase information are extracted. The rules are then applied to these features to calculate the probability of specific faults.
A significant advantage of rule-based analysis is its transparency. Unlike machine learning models, which can be difficult to interpret, rule-based systems offer clear, understandable reasoning behind each diagnosis. This is especially important in industrial settings where understanding the rationale for a decision is as crucial as the decision itself.
The Importance of Recording Phase Between Sensors
A standout feature of advanced rule-based systems is the ability to record and analyze phase information between sensors. Phase analysis is crucial in vibration diagnostics because it provides insights into the relationship between different parts of the machinery. For example, in cases of misalignment, the phase difference between vibration signals from different sensors can indicate the relative movement of components, helping to pinpoint the exact nature and location of the fault.
Moreover, phase analysis between two different accelerometers can reveal complex issues that might be missed by simpler amplitude-based measurements. Certain types of imbalance or misalignment produce specific phase relationships that are crucial for accurate diagnosis. Incorporating phase data into the diagnostic rules elevates the precision and reliability of fault detection.
Positive Predictive Value (PPV) and Negative Predictive Value (NPV)
In rule-based systems, not all diagnostic rules are equal. Positive Predictive Value (PPV) and Negative Predictive Value (NPV) are used to quantify the impact of each rule. These values represent the likelihood that a rule correctly identifies a fault when it is present (PPV) or correctly identifies the absence of a fault when it is not present (NPV).
A Medical Example: Diagnosing a Fracture
To illustrate PPV and NPV, imagine training a computer to diagnose a bone fracture. The rules might include:
- Pain in the region of the injury
- Loss of mobility
- Deformity of the arm or leg
- X-ray for confirmation
These rules are straightforward. Focusing on the first rule, pain in the region:
- PPV: Pain could indicate a fracture but might also result from a sprain or bruise. Thus, the PPV for this rule would be relatively low, as pain alone does not strongly predict a fracture.
- NPV: The absence of pain, however, strongly suggests the absence of a fracture, making the NPV for this rule quite high.
This example highlights how PPV and NPV assess the reliability of different diagnostic indicators in rule-based systems, including those used in vibration diagnostics.
From Medical Diagnostics to Vibration Analysis: Real-World Examples
While concepts like Positive Predictive Value (PPV) and Negative Predictive Value (NPV) are crucial in fields like medicine, they are just as important in vibration diagnostics. Let’s move from the medical analogy to explore two real-world examples of diagnosing mechanical faults: static imbalance and parallel misalignment. These examples demonstrate how rule-based analysis, coupled with phase measurement, can lead to accurate diagnoses, even when vibration patterns appear similar.
Example 1: Static Imbalance Diagnosis
In one case, we identified a static imbalance in a large industrial fan. The rules used were:
- RMS > reference value
- 1X > reference value
- 2X < 1X
- Vibration higher on fan side
- Phase between points close to 0°
Using ODS (Operating Deflection Shape) analysis, we visualized the vibration motion, which, along with the FFT showing a high 1X amplitude, pointed to an imbalance. The phase measurement confirmed the diagnosis by showing a 0° phase difference, typical of static imbalance.
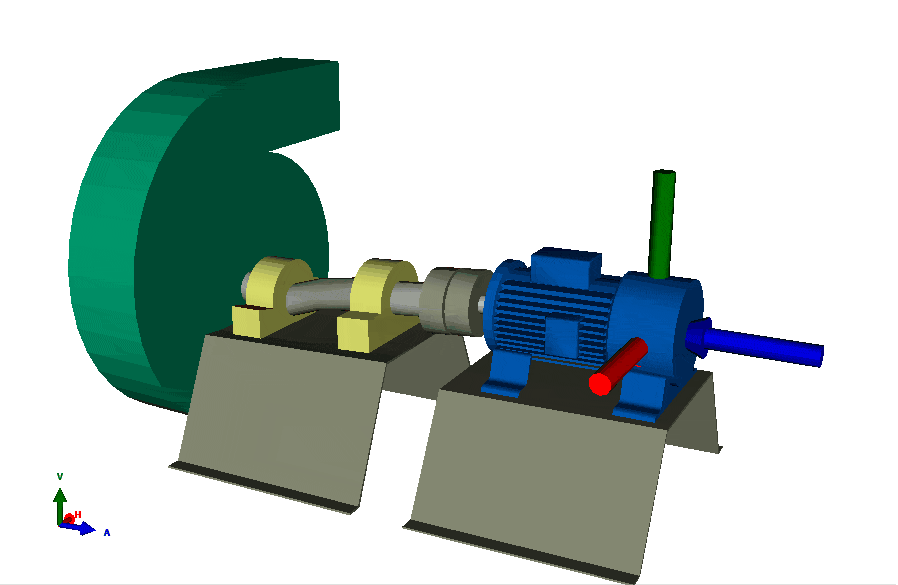
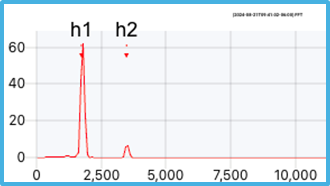
Example 2: Parallel Misalignment Diagnosis
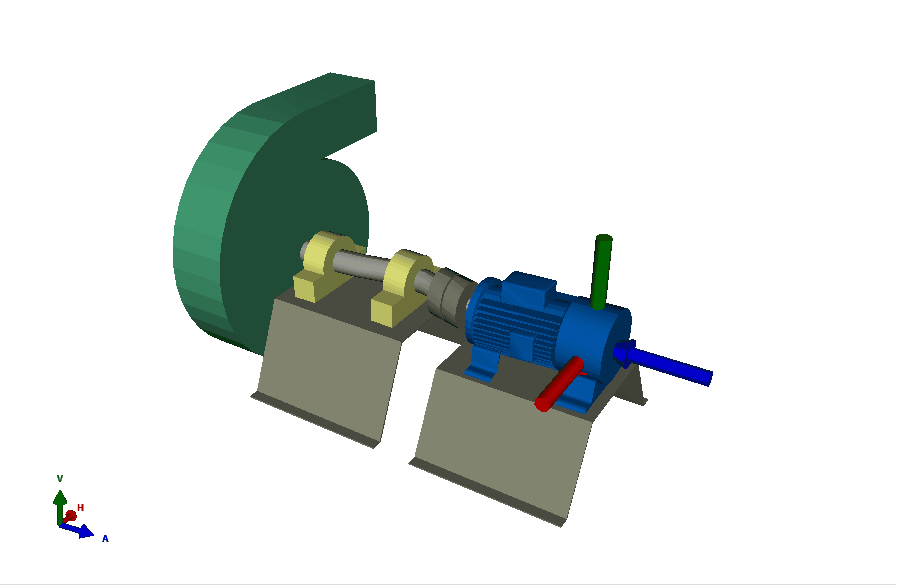
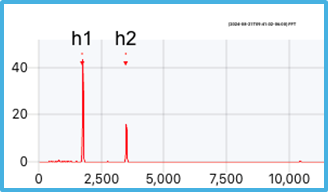
In another case, we diagnosed parallel misalignment. The rules were:
- RMS > reference value
- 1X > reference value
- 2X < 75% of 1X (This rule did not meet in this case)
- Max vibration on coupling side
- Phase between points 180°
Although the FFT data resembled that of the imbalance case in point 2 of the motor, the key difference was the phase measurement. The 180° phase difference between points confirmed the misalignment.
The Importance of Phase in Accurate Diagnostics
These examples show that while FFT data provides valuable insights, phase measurement is often the critical factor in distinguishing between similar faults. By combining rule-based analysis with phase data and ODS visualization, we can achieve precise and reliable diagnoses, preventing costly misinterpretations.
Understanding the Rule Editor for Diagnosing Static Imbalance
The rule editor interface you use allows you to set up diagnostic rules, such as for detecting static imbalance. Here’s a brief breakdown:
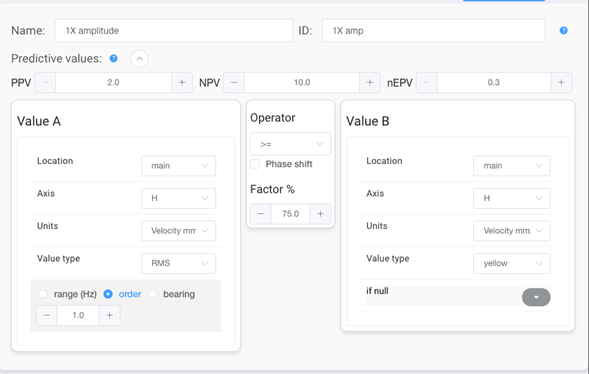
- Rule Name and ID: The rule is titled “1X amplitude,” focusing on the amplitude at the 1X frequency, corresponding to the machine’s rotational speed.
- Predictive Values:
- PPV (2.0): Indicates that if the rule is met (1X amplitude is high), it moderately supports the likelihood of a static imbalance.
- NPV (10.0): A high value suggesting that if the rule isn’t met (1X amplitude is low), static imbalance is very unlikely.
- Value A and Value B:
- Location & Axis: Both are set to “main” and “H” (horizontal axis), referring to where the vibration is measured.
- Units: Velocity in mm/s.
- Value Type:
- Value A: RMS amplitude within the 1X order (rotational frequency).
- Value B: A threshold, likely a cautionary level set to “yellow.”
- Operator and Factor %: The rule triggers if Value A is ≥ 75% of Value B.
How It Works
This rule checks if the 1X amplitude (a key indicator of static imbalance) exceeds a certain threshold. If it does, the system considers an imbalance moderately likely (PPV of 2.0). However, if the 1X amplitude is low, the system is confident (NPV of 10.0) that no imbalance exists. This ensures accurate diagnoses by strongly ruling out faults when critical indicators are absent.
Comparison with Machine Learning Models
Generalization vs. Specialization
Machine learning models excel at generalization, learning patterns across diverse datasets and adapting to new scenarios. However, this can also be a limitation, as ML models may overlook the nuances of specific machines or operating conditions. Rule-based systems, on the other hand, excel in specialization, offering superior accuracy and reliability within well-defined domains.
Transparency and Interpretability
Rule-based systems are inherently transparent, with each decision’s logic clear and understandable. This is critical for safety and reliability in industrial environments. In contrast, ML models, especially deep learning ones, can often act as black boxes—producing accurate results without clear reasoning, which can be a barrier to trust.
Adaptability and Scalability
ML models are more adaptable and scalable, applicable across various machinery and conditions without extensive reconfiguration. Rule-based systems require careful tuning and updating but provide unmatched precision in specific contexts.
The Hybrid Approach: Combining the Best of Both Worlds
In a hybrid model, rule-based analysis provides the foundational framework, built on expert knowledge and specialized rules proven effective in identifying faults. The system uses these rules to analyze vibration data, incorporating advanced features like phase analysis and probabilistic weighting with PPV and NPV.
Simultaneously, machine learning models enhance the system by recognizing patterns that may not be explicitly covered by the rule-based framework. When the system encounters a scenario outside predefined rules, the ML model steps in to provide a generalized diagnosis based on learned patterns.
This combination allows the hybrid system to maintain the precision and transparency of rule-based analysis while also benefiting from the adaptability and scalability of machine learning. The result is a diagnostic tool that is reliable, versatile, and accurate across a wide range of conditions.
Benefits of the Hybrid Approach
- Enhanced Accuracy: The hybrid system achieves higher diagnostic accuracy by combining rule-based precision with ML’s adaptability.
- Improved Trust: The transparency of rule-based analysis, combined with ML’s pattern recognition, builds trust in the system’s diagnoses.
- Scalability and Flexibility: The ML component allows the hybrid model to adapt to new data and conditions without constant rule updates, making it suitable for diverse industrial environments.
Conclusion
In the evolving landscape of vibration diagnostics, the debate between rule-based analysis and machine learning is shifting towards how to effectively combine them. Rule-based systems offer transparency, precision, and the benefit of decades of expert knowledge, while machine learning models provide adaptability and the ability to generalize across various conditions.
By integrating these two approaches we create The Green Doctor Technique, a hybrid model that delivers a diagnostic framework that is both reliable and interpretable, incorporating advanced capabilities of machine learning to handle a broader range of scenarios. As the industry continues to evolve, such hybrid systems are likely to become the gold standard in vibration diagnostics, offering enhanced accuracy, trust, and flexibility in predictive maintenance.
Dr. Thierry Erbessd, a prominent Mexican entrepreneur, and graduate of the National Polytechnic Institute has revolutionized the field of Vibration Analysis, Dynamic Balancing, and Condition Monitoring. Through his innovative software DigivibeMX®, DragonVision®, and WiSER Vibe®, he has set a before and after in the industry. As president of Erbessd Instruments®, he has not only led the company to the top of the global industrial maintenance industry but has also expanded its influence with strategically located offices in America, Europe, and Asia, establishing himself as an undisputed reference in industrial maintenance solutions worldwide.
ERBESSD INSTRUMENTS® is a leading manufacturer of Vibration Analysis Equipment, Dynamic Balancing Machines, and Condition Monitoring with facilities in Mexico, the USA, England, and India
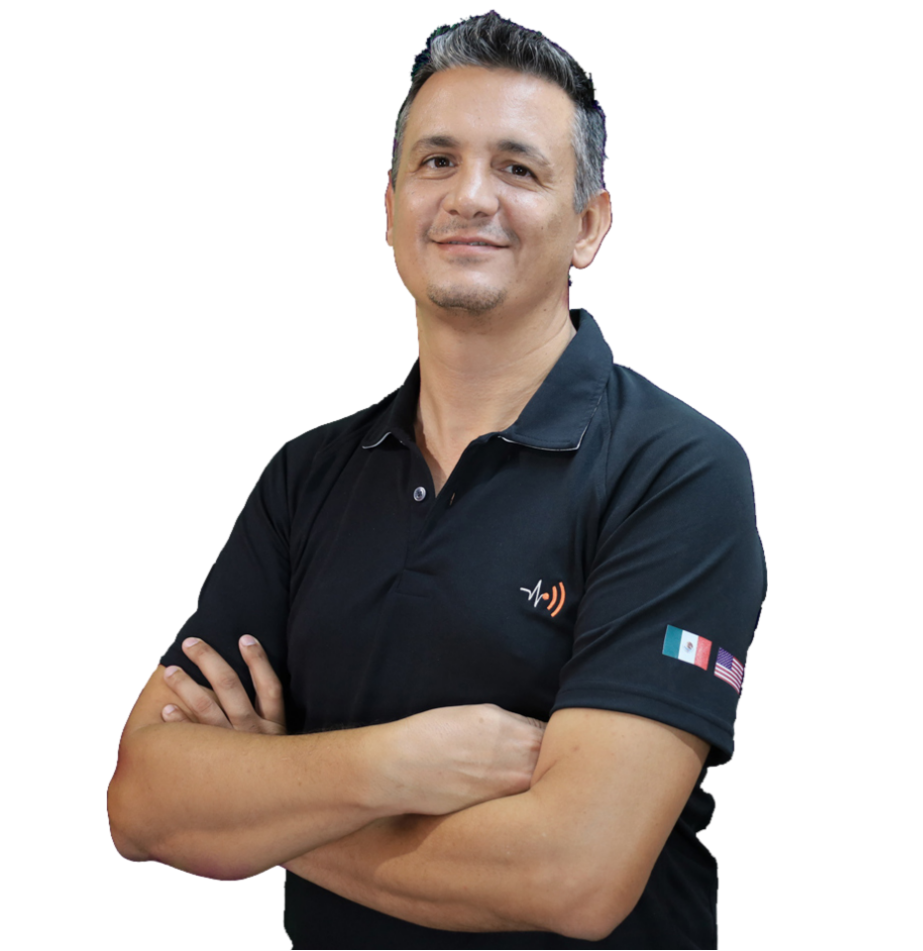