Balancing Rotating Machinery: Six Key Strategies
Balancing rotating machinery is essential in many industries, including manufacturing and power generation. Proper balancing ensures machines run smoothly, reduces wear, and extends their lifespan, ultimately saving on maintenance costs. This article outlines six essential strategies for effective balancing, focusing on critical steps in the process.
1. Identifying Imbalance
The first step is to accurately detect an imbalance. Using Fast Fourier Transform (FFT) analysis, vibrations of the machinery are analyzed by frequency components. An imbalance usually shows up at the machine’s fundamental frequency, with harmonics present but less intense. This pattern indicates an imbalance is causing the vibrations, signaling the need for corrective action.
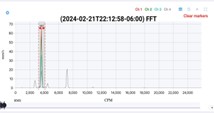
2. Cleaning Rotor Accumulations
Debris on blades or rotors can lead to imbalance. Especially in machinery like fans or mills that handle materials, it’s common for debris to alter mass distribution. Cleaning these parts thoroughly is crucial before balancing to prevent recurring imbalances due to new debris accumulation.
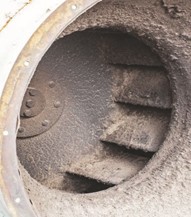
3. Checking for Mechanical Looseness
Mechanical looseness can cause and amplify vibrations, making balancing efforts ineffective. It’s important to detect and fix any looseness in the machine’s parts to ensure vibrations are due to imbalance and not abnormal movements.
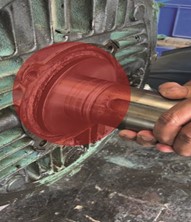
4. Addressing Resonance
Resonance amplifies vibrations when the machinery’s vibration frequency matches its natural frequency, complicating balancing efforts. Identifying and eliminating resonance may involve changing operating frequencies or installing dampers, requiring a deep understanding of the machine’s dynamics.
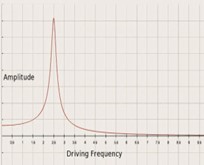
5. Detecting Bearing Failures
Bearing issues can mimic imbalance symptoms, showing abnormal vibrations. Before balancing, it’s vital to check bearings to ensure they’re not the problem source. Early bearing failure detection can prevent unnecessary balancing and avoid equipment damage.
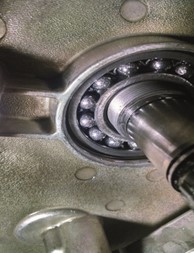
6. External Vibrations
External vibrations from the environment or other machines can interfere with balancing, and I like to refer to them as external vibration interference. These can cause a “beating” effect, where vibration amplitudes fluctuate. Identifying and managing this interference is key to effective balancing, sometimes requiring adjustments in the machinery setup or environment.
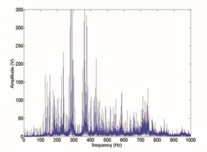
Conclusion
Effective machinery balancing is a complex process that goes beyond simple weight adjustment. It involves a comprehensive assessment of the equipment, its environment, and component dynamics. By implementing these six strategies, technicians can achieve not just immediate imbalance correction but also long-term machinery optimization. This approach enhances machinery reliability and efficiency, contributing to safer and more sustainable industrial operations.
Dr. Thierry Erbessd, a prominent Mexican entrepreneur, and graduate of the National Polytechnic Institute has revolutionized the field of Vibration Analysis, Dynamic Balancing, and Condition Monitoring. Through his innovative software DigivibeMX®, DragonVision®, and WiSER Vibe®, he has set a before and after in the industry. As president of Erbessd Instruments®, he has not only led the company to the top of the global industrial maintenance industry but has also expanded its influence with strategically located offices in America, Europe, and Asia, establishing himself as an undisputed reference in industrial maintenance solutions worldwide.
ERBESSD INSTRUMENTS® is a leading manufacturer of Vibration Analysis Equipment, Dynamic Balancing Machines, and Condition Monitoring with facilities in Mexico, the USA, England, and India
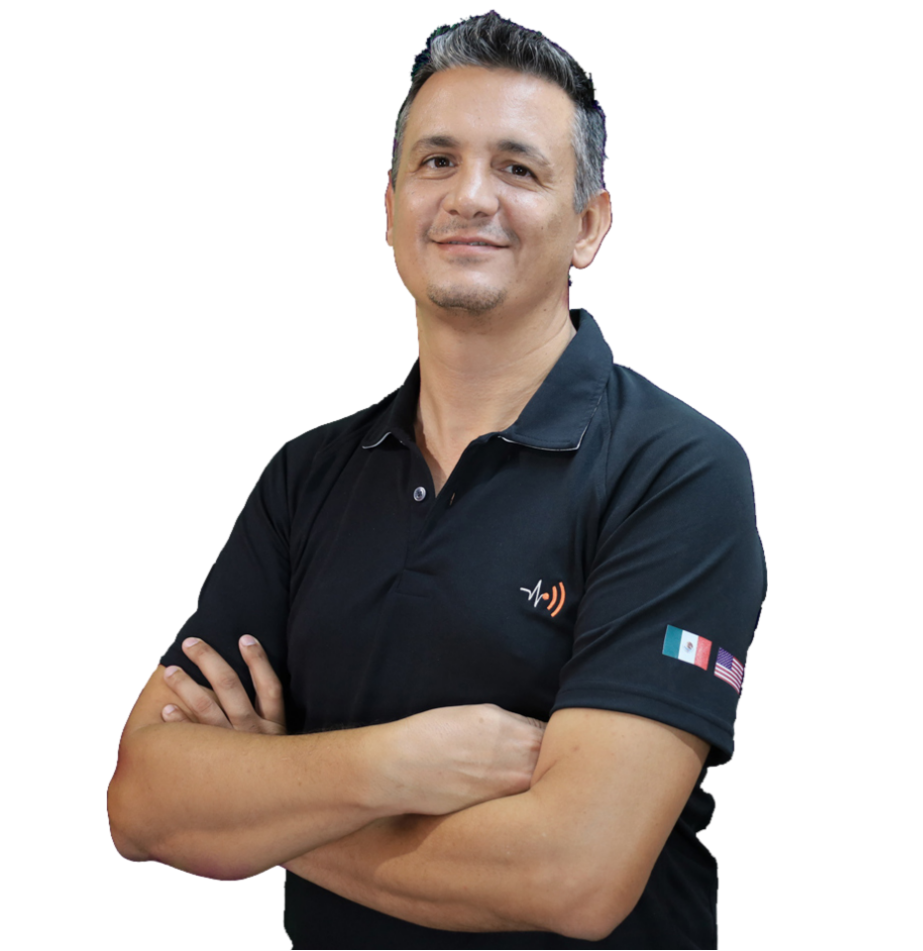