Remote Monitoring in Predictive Maintenance: Improving Machine Health
What is predictive maintenance?
Predictive maintenance is a proactive strategy that uses technology to monitor the condition of machines and equipment in real time, predicting when they might fail so that repairs can be made before any issues occur. Sensors are attached to the machines to collect information about their condition, such as temperature, vibrations, and sounds. This data is analyzed using special software that looks for signs of potential problems, like unusual noises or temperature changes. Based on this analysis, the software predicts when a machine is likely to have a problem, allowing maintenance work to be scheduled at a convenient time before any predicted issues actually occur.
Remote monitoring is a key part of predictive maintenance. It involves continuously checking important factors like vibration, energy use, speed, and temperature. This constant monitoring provides valuable data that helps identify potential problems early, reducing downtime and extending the life of the machines. Predictive maintenance is an important part of modern industry, improving productivity, efficiency, and competitiveness by ensuring machines work at their best.
The Importance of Predictive Maintenance
Predictive maintenance is crucial for keeping machines running smoothly by using data from remote monitoring sensors to predict and prevent potential problems. Advanced sensors and real-time data analysis help identify patterns and signs of trouble before they cause machine failure. This proactive approach allows maintenance teams to fix issues early, reducing unexpected downtime and ensuring continuous operation.
Key benefits of predictive maintenance
One of the main benefits of predictive maintenance is its ability to enhance productivity. By reducing the frequency and duration of equipment downtime, it ensures that machines are less likely to experience sudden failures. This keeps production processes running smoothly and efficiently, leading to higher output and better use of resources, which is essential in today’s fast-paced industrial environment.
Aditionaly, another important benefit is that predictive maintenance extends the lifespan of machinery. By catching and addressing issues early, it minimizes wear and tear on components, preventing major breakdowns and costly repairs. This not only saves money but also ensures that machines remain in good working condition for longer, maximizing their value and efficiency.
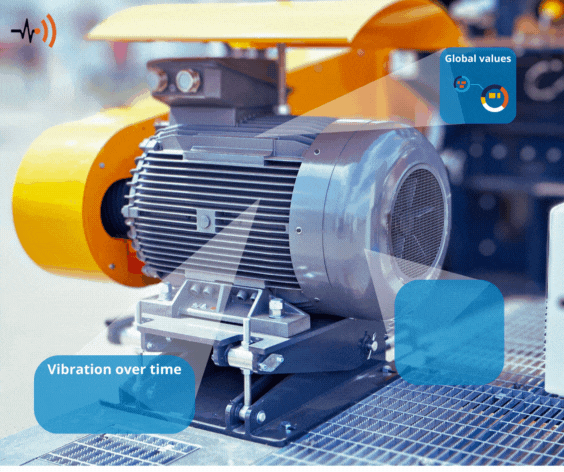
This not only saves money on maintenance and replacement costs but also ensures that machinery operates at peak performance for a longer period. Regular monitoring and maintenance also improve safety by reducing the risk of catastrophic failures that could endanger workers and equipment.
By incorporating predictive maintenance into their operations, companies can stay ahead of potential issues, ensure the longevity of their machinery, and achieve higher levels of productivity and efficiency. This forward-thinking approach is not only a cornerstone of Industry 4.0 but also a vital strategy for any organization looking to thrive in the modern industrial landscape.
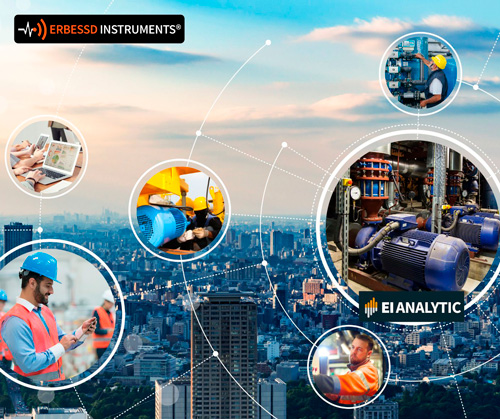
Sensing the world smartly
Smart sensors are well-suited for gathering data in remote monitoring systems. Their key feature is processing the measured value before sending it. While multiple data points might be read, only significant ones are sent, often when a threshold condition is met. This extends the battery life of wireless devices, making them ideal for remote monitoring.
Sensors are integral to monitor-based systems as they detect abnormal machine behaviors. Avoiding failures is vital to prevent downtimes in production. Common causes of machine failures include:
- Excessive vibration due to unbalance or damaged bearings
- Temperatures outside the optimal range
- Non-optimal rotational speeds for specific tasks
- Poor energy quality (voltage swells, dips, and transients)
Remote monitoring uses different sensors to prevent machine failures. You can mount tools like the Phantom System on the machine to receive critical information such as vibration, temperature, and speed. For instance, a wireless accelerometer can perform vibration analysis by sending data periodically or when an event is triggered.. If you also posses’ information about temperature, you can effectively perform a cross check to identify if the increase of temperature directly affects the vibration. Read about an interesting case study that exemplifies that correlation:
Read the case study
Turbo generator increases vibration only in the mornings
Multiple reports were received detailing significant increases in turbogenerator vibration during load operation. This concerning phenomenon became more evident at a specific period of the day, primarily between 5am and 9am. Reports of vibration increases were persistent and the severity of these initial details became a cause of great concern to all involved in the operation and maintenance of the turbogenerator.
Faced with this situation, a strategic decision was made to conduct a thorough and meticulous vibration analysis. The main objective of this analysis was to identify the underlying causes of the vibration increases, in order to thoroughly understand the nature of the problem and develop effective and lasting solutions to address it.
The Phantom System
The Phantom system offers a comprehensive smart sensing solution using Bluetooth Low Energy (BLE) technology and ultra-long battery life. It visualizes important parameters like vibration, temperature, voltage, and RPM data collected from any machine, ensuring continuous monitoring to avoid downtimes that could compromise customer delivery times. This advanced system can also monitor additional parameters such as pressure, proximity, oil condition, and more, providing a holistic view of your machine’s behavior.
The more data you collect, the better your predictive maintenance capabilities. Extensive data collection allows for more accurate predictions of potential issues, enhancing the reliability and efficiency of your machinery. However, simply collecting data is not enough; transforming data into actionable insights requires powerful analytical tools. To properly process the values you collect, you need high-quality software solutions that can analyze and interpret the data effectively.
The Phantom system’s integration with top-tier software, like DigivibeMX or EI-Analytic, ensures that the vast amounts of data collected are converted into meaningful information, enabling informed decision-making. This comprehensive approach to data collection and analysis is crucial for maintaining optimal machine performance, preventing unexpected downtimes, and ensuring timely deliveries. Investing in the Phantom system means leveraging advanced technology to enhance predictive maintenance, align with Industry 4.0 standards, and achieve superior operational efficiency.
The importance of software for remote monitoring and predictive maintenance
In the realm of remote monitoring and predictive maintenance, software plays a pivotal role in transforming raw data into actionable insights. The effectiveness of predictive maintenance hinges not only on the quality of the sensors and the data they collect but also on the software’s ability to process and analyze this data. High-quality software solutions are essential for several reasons:
Data Integration and Analysis
Predictive maintenance involves monitoring various parameters such as vibration, temperature, amperage, RPM, pressure, proximity, and oil condition. The software must integrate data from multiple sensors and sources to provide a comprehensive view of machine health. Advanced algorithms and analytical tools within the software can identify patterns and anomalies that indicate potential issues. This capability is crucial for predicting failures before they occur, allowing for timely maintenance and repairs.
Real-Time Monitoring and Alerts
Effective predictive maintenance software provides real-time monitoring and alerts. It continuously analyzes incoming data, comparing it against predefined thresholds and historical trends. When the software detects an anomaly or a condition that deviates from normal parameters, it triggers an alert. These real-time alerts enable maintenance teams to respond quickly, preventing minor issues from escalating into major failures. Real-time monitoring also ensures that the machinery operates within optimal parameters, enhancing performance and efficiency.
Data Visualization
Visualization tools are critical components of predictive maintenance software. They present complex data in an easily understandable format through dashboards, charts, and graphs. Effective visualization helps maintenance teams quickly grasp the status of machinery and identify trends or patterns that require attention. Visual tools also facilitate communication among team members and stakeholders, ensuring that everyone has a clear understanding of the machine’s health and performance.
Historical Data and Trend Analysis
Analyzing historical data is fundamental for predictive maintenance. The software must store and manage large volumes of data, allowing for long-term trend analysis. By examining historical trends, the software can predict future failures and optimize maintenance schedules. Historical data analysis also helps in identifying recurring issues and understanding the root causes of machine problems, leading to more effective and targeted maintenance strategies.
There are several options that you can explore to find the software that suits your need. See below for some great examples:
Accesing data from the cloud
In remote monitoring, proper network management is essential. Storing data is crucial for generating trends on machine performance. Databases are commonly used for this purpose, but cloud-based services offer a higher level of accessibility than local database servers. Engineers can monitor machinery from different production plants worldwide.
Data handling in remote monitoring systems must be done carefully to prevent loss that could ruin analysis. High-quality software is necessary to ensure correct data analysis.
The interconnectivity of devices and digitalization are key goals in Industry 4.0. A robust remote monitoring system should comply with these guidelines, integrating smart sensors and advanced data storage/display software to form a complete system for remote monitoring and data analysis.
Give a look to our powerful cloud-based service for machine condition monitoring
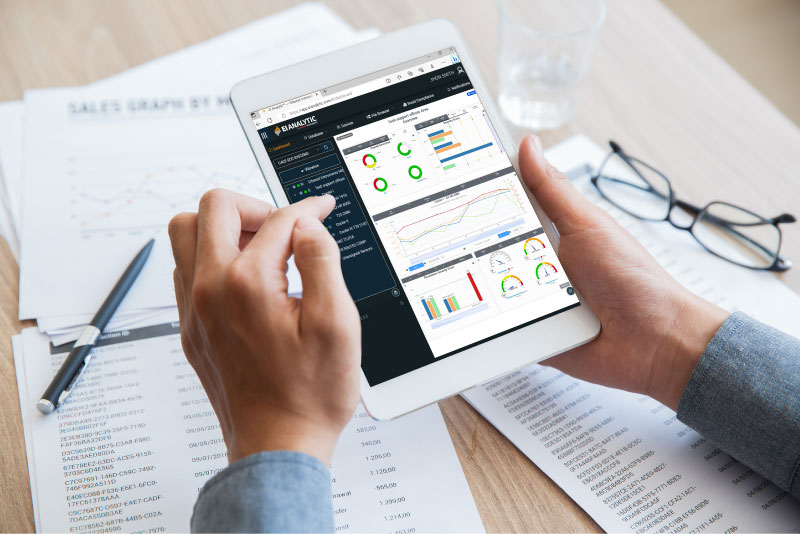
Start predicting now
In conclusion, remote monitoring and predictive maintenance are vital for preventing machine failure and ensuring optimal performance in modern industrial operations. By leveraging advanced technologies like smart sensors and robust software, organizations can monitor key variables such as vibration, temperature, amperage, and RPM in real-time. This proactive approach minimizes downtime, enhances productivity, and extends the lifespan of machinery.
Integrating predictive maintenance within the Industry 4.0 framework provides significant competitive advantages. The Phantom system exemplifies this by combining Bluetooth Low Energy (BLE) technology with ultra-long battery life, offering continuous monitoring and comprehensive data collection. However, the true value lies in analyzing this data effectively with high-quality software, which provides real-time alerts, visualization, and advanced analytics.
Investing in advanced remote monitoring systems and predictive maintenance solutions is essential for optimizing maintenance schedules, reducing downtime, and improving overall efficiency. Embracing these technologies ensures machinery operates at peak performance and supports sustainable operational excellence in the era of Industry 4.0.
Luis Sabido works as the Head of Customer Service and Technical Support at Erbessd Instruments. He is an experienced professional with 5 years of experience helping Erbessd Instruments’ customers worldwide master the health of their machines. Luis has studied Physics Engineering and is currently pursuing a second degree in Engineering in Technology and Information Systems.
ERBESSD INSTRUMENTS® is a leading manufacturer of Vibration Analysis Equipment, Dynamic Balancing Machines, and Condition Monitoring with facilities in Mexico, the USA, England, and India
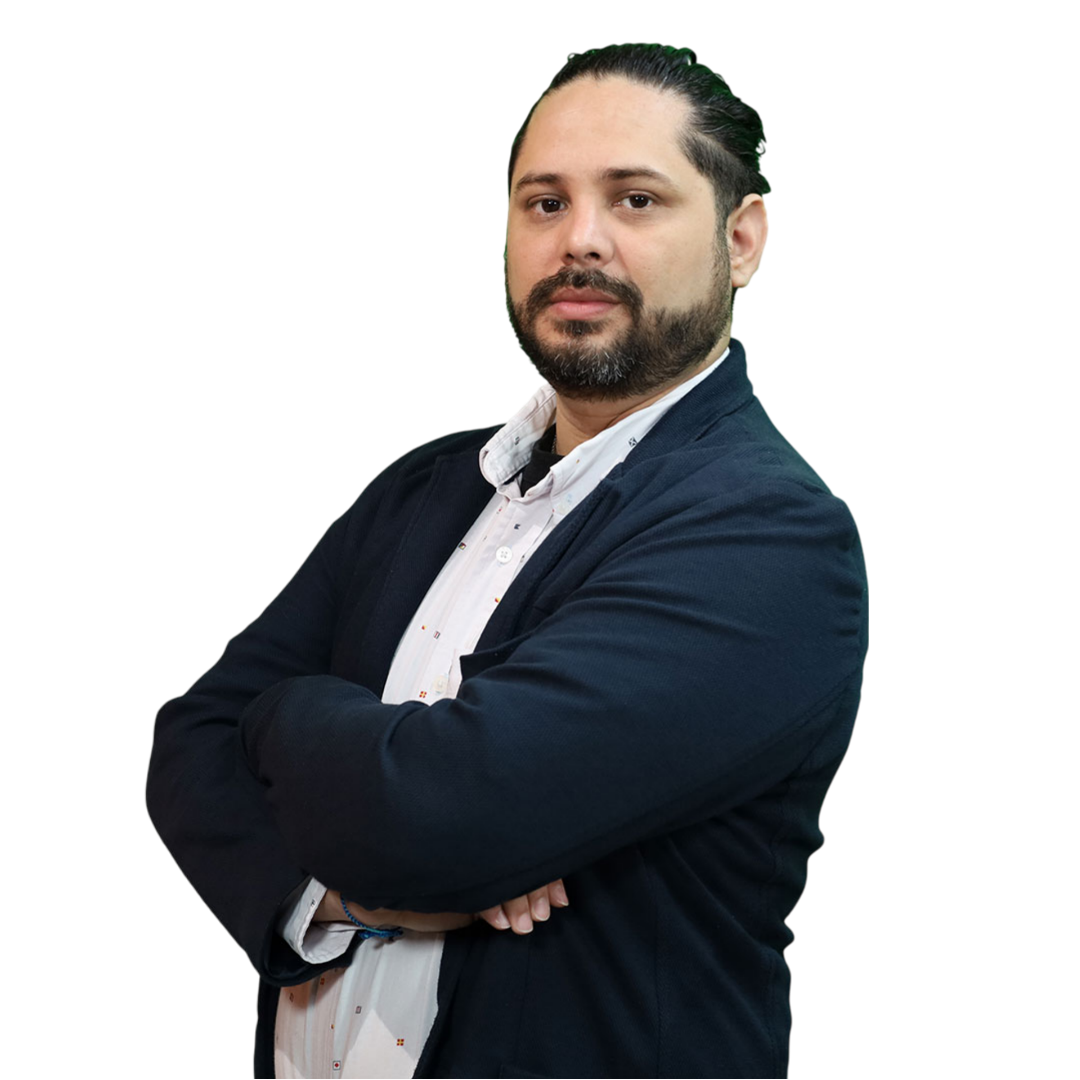