
Harnessing the Power of Vibration Analysis: Unveiling its Multifaceted Benefits
In the realm of modern industrial maintenance, vibration analysis has emerged as a critical tool for ensuring the smooth and efficient operation of machinery. This technique, which involves monitoring and analyzing the vibration patterns of equipment, has proven to be invaluable across various industries. Here, we delve into the comprehensive benefits of vibration analysis, highlighting its role in enhancing equipment reliability, improving safety, and optimizing maintenance strategies.
1. Proactive Maintenance and Increased Equipment Reliability
One of the primary benefits of vibration analysis is its ability to enable proactive maintenance. By regularly monitoring the vibration signatures of machinery, potential issues can be identified long before they escalate into serious problems. This early detection allows for timely interventions, such as bearing replacements or lubrication, preventing catastrophic failures and unplanned downtime.
Vibration analysis helps in identifying:
Imbalance: When a rotating component’s mass is unevenly distributed, it causes excess vibration, leading to wear and tear.
Misalignment: Misaligned shafts or couplings can produce abnormal vibrations, reducing the lifespan of equipment.
Bearing Faults: Detecting bearing wear or damage through vibration patterns can prevent more severe damage to machinery.
Looseness: Components that are not securely fastened can generate vibrations, indicating a need for tightening.
By addressing these issues proactively, companies can significantly increase the reliability and longevity of their equipment, ensuring consistent production and reducing the risk of unexpected breakdowns.
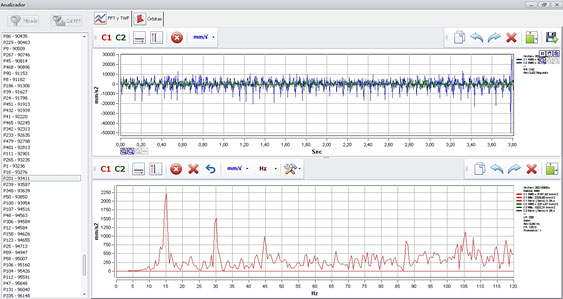
2. Cost Savings through Optimized Maintenance
Implementing vibration analysis as part of a predictive maintenance strategy can lead to substantial cost savings. Traditional maintenance approaches, such as reactive and scheduled maintenance, often result in unnecessary repairs or overlooked issues. In contrast, vibration analysis allows for condition-based maintenance, where interventions are performed only when necessary.
The financial benefits include:
Reduced Repair Costs: Early detection of faults minimizes the extent of damage, leading to lower repair costs.
Extended Equipment Lifespan: By maintaining optimal operating conditions, machinery components last longer, reducing the need for frequent replacements.
Minimized Downtime: Scheduled maintenance can be planned during non-productive hours, minimizing production losses.
Efficient Resource Allocation: Maintenance efforts are focused on actual needs, optimizing labor and material usage.
Companies can reinvest these savings into other areas of their operations, fostering growth and innovation.
3. Enhanced Safety and Compliance
Safety is paramount in any industrial setting, and vibration analysis plays a crucial role in maintaining a safe working environment. Machinery failures can lead to hazardous conditions, including equipment malfunctions, fires, or explosions. By identifying and addressing issues before they pose a safety risk, vibration analysis contributes to a safer workplace.
Benefits for safety and compliance include:
Preventing Accidents: Detecting and fixing faults reduces the likelihood of accidents caused by machinery failure.
Compliance with Regulations: Many industries are subject to stringent safety regulations. Vibration analysis helps in meeting these standards by ensuring equipment operates within safe parameters.
Worker Protection: A safer environment protects workers from injury, fostering a culture of safety and well-being.
Companies that prioritize safety through practices like vibration analysis not only protect their workforce but also avoid potential legal and financial repercussions associated with safety violations.
4. Improved Energy Efficiency
Another significant advantage of vibration analysis is its contribution to energy efficiency. Machines operating under optimal conditions consume less energy, reducing operational costs and environmental impact.
Key points on energy efficiency include:
Identifying Inefficiencies: Vibration analysis can detect imbalances or misalignments that cause machinery to work harder than necessary, leading to higher energy consumption.
Optimizing Performance: Regular monitoring ensures machines are running at peak efficiency, conserving energy.
Environmental Impact: Reduced energy consumption translates to a smaller carbon footprint, supporting sustainability initiatives.
By maintaining equipment at optimal performance levels, companies can achieve substantial energy savings and contribute to environmental conservation.
5. Data-Driven Decision Making
The insights gained from vibration analysis provide a wealth of data that can inform maintenance and operational decisions. This data-driven approach allows companies to make informed choices based on actual equipment conditions rather than relying on assumptions or reactive measures.
Advantages of data-driven decisions include:
Precision Maintenance: Maintenance schedules are based on real-time data, ensuring interventions are timely and necessary.
Trend Analysis: Historical vibration data helps in identifying trends and patterns, enabling predictive maintenance and long-term planning.
Performance Optimization: Data can reveal areas for improvement, leading to enhanced performance and efficiency.
By leveraging the data from vibration analysis, companies can optimize their maintenance strategies, improve operational efficiency, and make strategic investments in their machinery.
Conclusion
Vibration analysis is a powerful tool that offers a multitude of benefits, from enhancing equipment reliability and safety to driving cost savings and energy efficiency. Its role in modern industrial maintenance is indispensable, providing the insights needed for proactive and data-driven decision-making. As industries continue to evolve and prioritize efficiency and sustainability, the adoption of vibration analysis will undoubtedly become even more widespread, ensuring the continued success and longevity of industrial operations.
Dr. Michael Howard, is an American entrepreneur and Air Force veteran with a remarkable career in the predictive maintenance industry spanning over 30 years, and a variety of industrial sectors, including industrial manufacturing, reliability engineering, and instrumentation development and design organizations. Dr. Howard is a graduate of Excelsior University, Capella University, and New Charter University with degrees in Electro-Mechanical Engineering, Leadership and Organizational Management, and Engineering Management.
As the CEO of Erbessd Instruments, he leads strategy, sales, marketing, and operations in English-speaking markets. He is a certified reliability engineer, certified maintenance and reliability professional, and category III vibration analyst. Michael is a passionate advocate for wireless instrumentation, video deflection, and the Industrial Internet of Things (IIoT).
ERBESSD INSTRUMENTS® is a leading manufacturer of Vibration Analysis Equipment, Dynamic Balancing Machines, and Condition Monitoring with facilities in Mexico, the USA, the United Kingdom, and India.
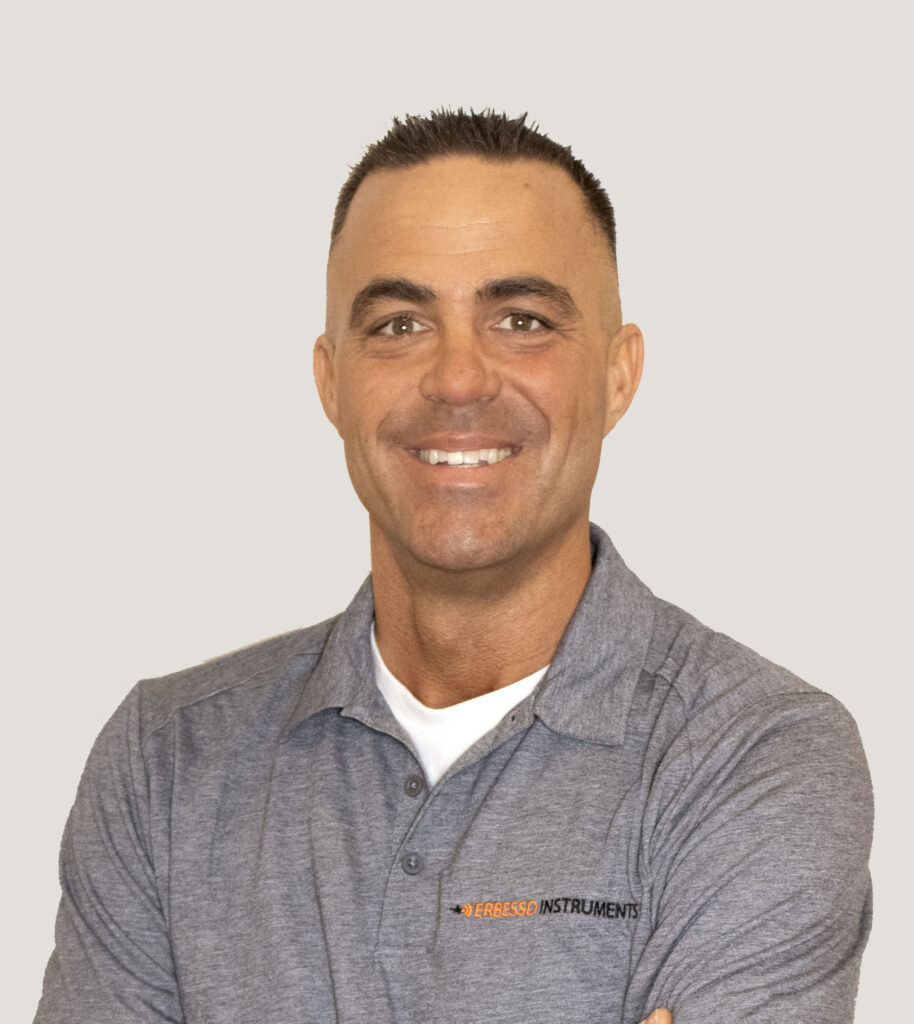