Finding the Best Vibration Analyzer
Finding the best Vibration Analyzer for your application can be quite tricky. Moreover, if you don’t know how to identify the functionality that you need.
So, what is a vibration analyzer? And more importantly, what do I need to know before I chose one. Take some time to read this post and find out your best option.
What is a Vibration Analyzer?
A Vibration Analyzer is an instrument used to measure, store and diagnose the vibration produced by machinery. It uses FFT based tools to display the magnitude of the vibration as it varies over the frequency. The primary use is to identify and predict faults in industrial machines, as well as the causes that originate them.
The Best vibration analyzers are capable of saving measurements and organizing them for future analysis, thus, generating trends for each machine. These instruments are also known as data collectors.
Meet Our Vibration Analyzers
DigivibeMX® 11 M30: The Most Complete Vibration Analyzer
A Vibration Analyzer used to measure, store and diagnose the vibration produced by machinery. It uses FFT based tools to display the magnitude of the vibration as it varies over the frequency. The primary use is to identify and predict faults in industrial machines as well as the causes that originate them.

Phantom® Vibration Analyzer
Phantom is a Wireless Vibration Monitoring System that integrates other parameters such as temperature, current, RPM and speed into a single diagnosis system. Some of our vibration sensors have a battery life that lasts enough to take up to 100,000 measurements, and they are very easy to install. Equally important, Phantom can send data to a local database or to our cloud-based system, EI-Analytic™. At any moment, you can keep track of your machinery using any device such as a smartphone, computer or tablet.
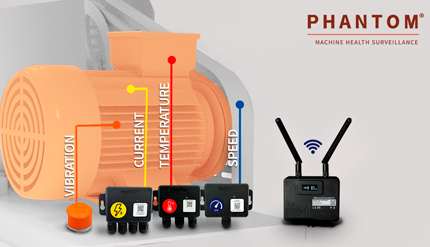
Mobile Vibration Analizer: WiSER Vibe
WiSER® Vibe is the iOS and Android application that allows you to take vibration data on the go. Place your WiSER™ or Phantom® on your machine and connect to it using your iOS or Android device.
You now have a complete vibration analysis in the palm of your hand. With this app you have 2 million resolution lines, you can store data in your portable device, send data through email or send it directly to the EI-Analytic cloud, record multiple parameters and up to 4 vibration channels. Compatible with EI WiSER®, WiSER® 3X, GX400 and now it’s also compatible with Phantom® vibration sensors.
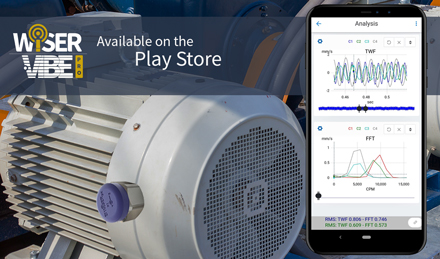
Dragon Vision™ Video Vibration Analyzer
Dragon Vision uses a reference accelerometer signal and a mapping accelerometer in order to generate motion magnification maps amplifying the movement detected with the accelerometer and showing the result on photos of the measured equipment. The more measuring points you feed into the program, the amplified vibration map will have higher resolution, and you will be able to see more details. With the help of any accelerometer, you can detect up to 15,000 Hz in any axis and with very high precision. You’ll be able to detect bearing issues, gearbox problems and many more.
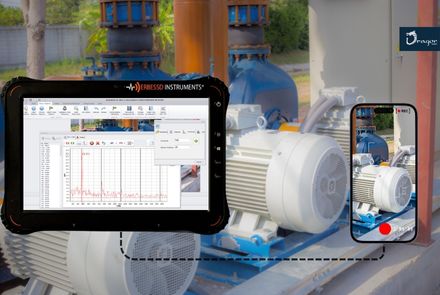
Vibration Analyzer DigivibeMX® 11 M20
M20 can cover your most basic vibration analysis needs. Compatible with WiSER and GX400 you can take advantage of the capabilities that the most reliable Vibration Analysis software has to offer. You can access tools like 3D Waterfalls, Route Analysis, Tendency curves, database compatibility and synchronization. You can also choose to upgrade your analysis to M30 and use the complete functions included in DigivibeMX® 11; such as Phantom and balancing capabilities
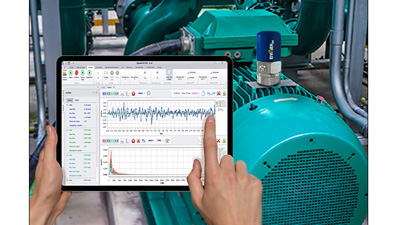
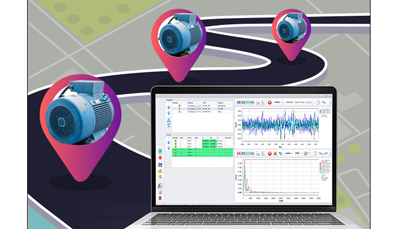
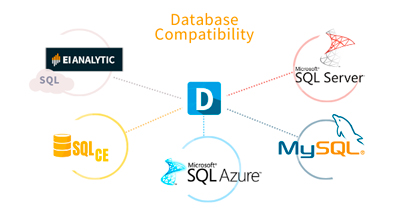
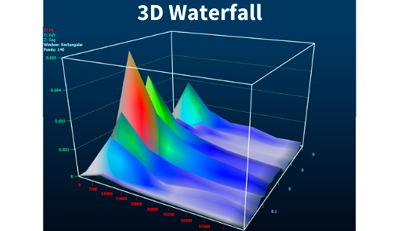
How does a vibration analyzer work?
A Vibration Analyzer is basically a computer that records vibration through one or more accelerometers. Vibration motion, inside the accelerometer, is converted into an electrical current proportional to the acceleration. This signal is stored and processed in the computer to display its magnitude versus frequency with an algorithm called FFT (Fast Fourier Transform).
Features of a Vibration Analyzer
When choosing a vibration analyzer, the following are the main features to focus on:
- Number of input channels
- Lines of resolution
- Resolution
- Frequency range
- Additional functions like Balancing, ODS (3D simulations)
- Types of sensors that it can handle
- Portability
- Technical support and spare parts
- Price and Annual costs (if applied)
You can find vibration analyzers on the market with different number of input channels, the most common being 2 to 4 channels.
Recording 2 channels simultaneously is usually enough for functions like balancing, phase analysis, Bode graph and ODS (these functions will be explained in another article). On the contrary, the use of a triaxial accelerometers as well as 2 simultaneous planes balancing requires 4 channels.
Single channel analyzers are not common anymore since they are unable to perform necessary techniques necessary for some of the most important faults, like misalignment, Bode and balancing.
The number of lines of resolution defines how many points will integrate the spectrum. Although the correct term should be “Points”, the word “Lines” are still used probably because it was created for in audio FFT which were plotted with bars (or lines).
The lines of resolution are sometimes wrongly associated with the resolution of a spectrum; however, this is not entirely correct. The LR does not distinguish between a large or short frequency range, thus, having a lower frequency range will show a better resolution and higher range with the same amount of lines. Observe the following example:
Example 1
Suppose we select 6400 LR, let’s see these 2 examples:
Max Frequency of 10,000 Hz: 10,000 / 6,400 = 1.56 Hz (93 CPM)
Max Frequency of 1,000 Hz: 1,000 / 6,400 = 0.156 Hz (9.3 CPM)
The second example will show 10 times the resolution of the first one.
In other words, you will look for precision in a spectrum when you need to differentiate between two frequencies that are close to each other.
Example 2
Imagine a fan with pulley transmission in which the pulleys have very similar diameters and thus work at few RPMs between each other.
To distinguish the imbalance of the motor from the fan, you will need enough resolution to get the two frequencies to show in independent peaks in the FFT and therefore measure the amplitude of each one. In case your maximum resolution lines were of 6,400 you would have to sacrifice your maximum frequency having to set a range of 200 to 400 Hz and thus not seeing the full range of the accelerometer
In conclusion, the lines of resolution are a very important factor in the choice of the best Vibration Analyzer since your resolution and frequency range are extremely related to it. Hence, the analyzers capable of calculating millions of lines of resolution will rarely have to sacrifice frequency range to achieve excellent resolution.
The frequency range of a vibration analyzer is determined by two factors: the highest sample rate of the analyzer and the maximum frequency that the accelerometer can measure. The Sample Rate is the amount of measurements that a system can perform within 1 second. Thus, the maximum frequency that this device can see will be half of its sampling rate.
As an example, a system that samples at 20 kHz will have a maximum frequency of 10 kHz[i]. Think of it this way, if we had a signal of 1 Hz (1 cycle per second), to be able to see its wave form, that is to say in its negative part and in the positive part we would have to make a measurement at least 2 times per cycle.
Accelerometers, on the other hand, have a maximum and minimum frequency (usually 1 Hz to 10 kHz) that they can measure accurately. Outside these limits, the sensitivity can be progressively different, so it is not recommended to make measurements outside their range.
Generally speaking, the frequency range of an analyzer is usually higher than the frequency range of conventional accelerometers, but having a wide range will give us the freedom to connect sensors with higher ranges.
[i]In fact for this calculation we should be using Nyquist frequency which we will see in another article. But this means that the real divisor is 2.56 instead of 2.
Are you still here? Excellent now pamper yourself a little and go grab some cookies or gummy bears, because it gets better.
Finally! we got to the part that I like the most. The functions of the analyzers are probably the part that changes the most between one analyzer and another. I will start by listing the most important functions that every analyzer has, or at least should have and these are.
FFT
Spectrum, is the heart of an analyzer, almost all analysis functions need it inside their calculation. Not to mention FFT measurement tools and Window functions: Rectangular, Hann, Hamming, Flat Top.
Time Wave Form
Vibration analyzers draw this chart with the signal as it arrives from the sensor. It is not used very often, however some secondary functions like Circular Time Wave Form are useful to detect patterns in gearboxes or bearings.
Measurement parameters
Aceleración, Velocidad, Desplazamiento y Envolvente de Aceleración (demodulación o equivalente, útil para detectar fallas tempranas en rodamientos).
Machinery database
Will store all the information related to your machines and all your recordings over time.
Vibration Data Collector
A good vibration analyzer should also be a vibration data collector. At least it should have a mechanism to store and organize the recordings of the machines to store a history and trend of the machinery. This is one of the main factors to consider because consider that you will be dealing with this part of the system EVERY day. Having an intuitive and easy-to-use database interface is vital to avoid wasting time later.
Envelope Alarms
The theory tells us the ideal vibration levels for some of the machinery in the industry, but what will you do if you do not know what the ideal value is? This tool will let you know the moment the vibration increases in any of its frequencies. It wraps the full spectrum and rings an alarm whenever any frequency grows more than the percentage you configured.
Report Tools
Reports can be very tedious if you create signal by signal, value by value. Automatic reporting saves considerable time.
Phase Analysis
Phase analysis requires you to record at least 2 channels simultaneously in order identify the direction of motion compared to each other. This function is mandatory to fully diagnose misalignment among some other faults.
Bearing database
This function is important because bearing vibration analysis identifies fault frequencies related to bearing geometry. Thus, you have a complete bearings database to obtain manufacturer information to perform fault calculations.
Dynamic Balancing
Dynamic balancing is a functionality which is present in the vast majority of equipment usually as optional, however, considers that imbalance is one of the most common causes of vibration in the machinery, wouldn’t it be good to correct the problem instantly?
The advanced functions may or may not be present on many systems, or could have different names than those I will mention.
ODS
(Operating deflection shapes) Simulates the movement of the whole machine in a 3D drawing. This is a tool that is not so common, but is excellent for diagnosis and above all, it is very easy to understand for anyone, even people with little or no knowledge of vibration analysis. ODS is also undoubtedly a very attractive tool that sells for being so descriptive.
Some new vibration analyzers offer already a cloud based database to be shared with your customers. Sharing your vibration database with your customers, not only will it make your life easier reducing the amount of reports, but also it will give your customers the satisfaction of having the best technology available.
Accelerometers
The output voltage is proportional to the acceleration of the vibration. Most of these sensors require a power supply because they contain small amplifiers and filters to eliminate noise.
Vibration Analyzers most commonly use Accelerometers due to their excellent frequency and amplitude range as well as the low noise they generate. In return, they convert acceleration into other parameters like velocity and displacements, which are more frequently used in vibration analysis.
Velocimeter
Its signal is proportional to the velocity of the vibration. They are electromagnetic sensors, so they do not require power.
Displacement probes
The output signal is proportional to the displacement of the vibration. They are usually non-contact sensors, so they are ideal for measuring vibrations and eccentricity of shafts.
It is convenient that the vibration analyzer you choose has the possibility to connect other types of sensors. There are machines for which simply the accelerometer is not the appropriate tool. Oil bearings are an example of the above because oil dampens the vibrations, thus, making its measurement with accelerometers less reliable.
Take in account the portability of an analyzer since you will be dealing with this every day. On the other hand, you must also consider that a small device with little functionality will be a big limitation.
In terms of portability, the general types of analyzers are the following
Pen type
People use these usually only to measure vibration RMS, the functionality is usually very pour, although they have the great advantage that they fit everywhere, even in your pocket.
Hand-held
They are devices the size of a cell phone, have a larger screen, show the spectra and are well prepared for taking routes. They are very portable and comfortable for use. These vibration analyzers usually have slow processors, so the number of lines of resolution, memory and functions is reduced, thus requiring PC based software to complement functionality.
Propriety Tough Devices
They range from the size of a cell phone to beyond the size of a tablet but with a greater thickness. They are the most common and are a fair choice for industrial use. There are many brands and with very variable functionality.
The disadvantage is that they are not universally used devices and, thus, the cost of manufacturing them is high. This makes them have slow processors and low memory. This condition can make these systems less functional.
It is complicated to know what kind of processors these devices have because it rarely appears in the technical file. Our best approach will be to evaluate trough the amount of memory and functions of which they presume. The good news is that most of these computers have PC software to make an analysis of the data collected easier. We just need to be aware of the cost of this software.
Tablets and PC
They are becoming more popular due to the huge power and memory of new computers. Updating the computer generates no cost while installing the software and also portability in commercial tablets increases on every new model.
A small disadvantage is that most of them are not sweated for industrial environments, however, Windows and Android rugged tablets are available at very affordable prices without the need to by tied to a brand.
In the best vibration analyzer, support is a very important aspect because, let’s face it. Nothing is ever perfect and we always need assistance for complex devices. Thus, you will need to be in contact with the distributor or the manufacturer of the product with certain frequency. The most important points to take into account for technical support are:
Cost
Is there an additional cost for support?
Speed
Speed to answer our questions.
Shipping time for spare parts.
If you do not have backup system, you will have the equipment broken for more than a month which will surely cause delay in your production or services.
Contact
Possibility of speaking by telephone with the technical team.
Último pero no menos importante, el precio es uno de los principales factores a Last but not least, price is one of the main factors to take in account. Understand how you will be charged, this is vital to calculate our financial capacity for acquisition. Points to consider:en cuenta, Entender como se te cobrará es vital para calcular nuestra capacidad financiera de adquisición. Puntos a tener en cuenta:
Price
Identify the price of the system as well as needed accessories, software and other possible features.
Annuity
In some cases, you need to consider an annual license fee for support. Check before you buy.
Cost of spare parts
Do not forget that at some point you will have to change a cable, a sensor, or the complete module, so I recommend you to be sure it is within your possibilities.
Update cost
Most brands update their equipment regularly, check the costs of these updates.
Dr. Thierry Erbessd, a prominent Mexican entrepreneur, and graduate of the National Polytechnic Institute has revolutionized the field of Vibration Analysis, Dynamic Balancing, and Condition Monitoring. Through his innovative software DigivibeMX®, DragonVision®, and WiSER Vibe®, he has set a before and after in the industry. As president of Erbessd Instruments®, he has not only led the company to the top of the global industrial maintenance industry but has also expanded its influence with strategically located offices in America, Europe, and Asia, establishing himself as an undisputed reference in industrial maintenance solutions worldwide.
ERBESSD INSTRUMENTS® is a leading manufacturer of Vibration Analysis Equipment, Dynamic Balancing Machines, and Condition Monitoring with facilities in Mexico, the USA, England, and India
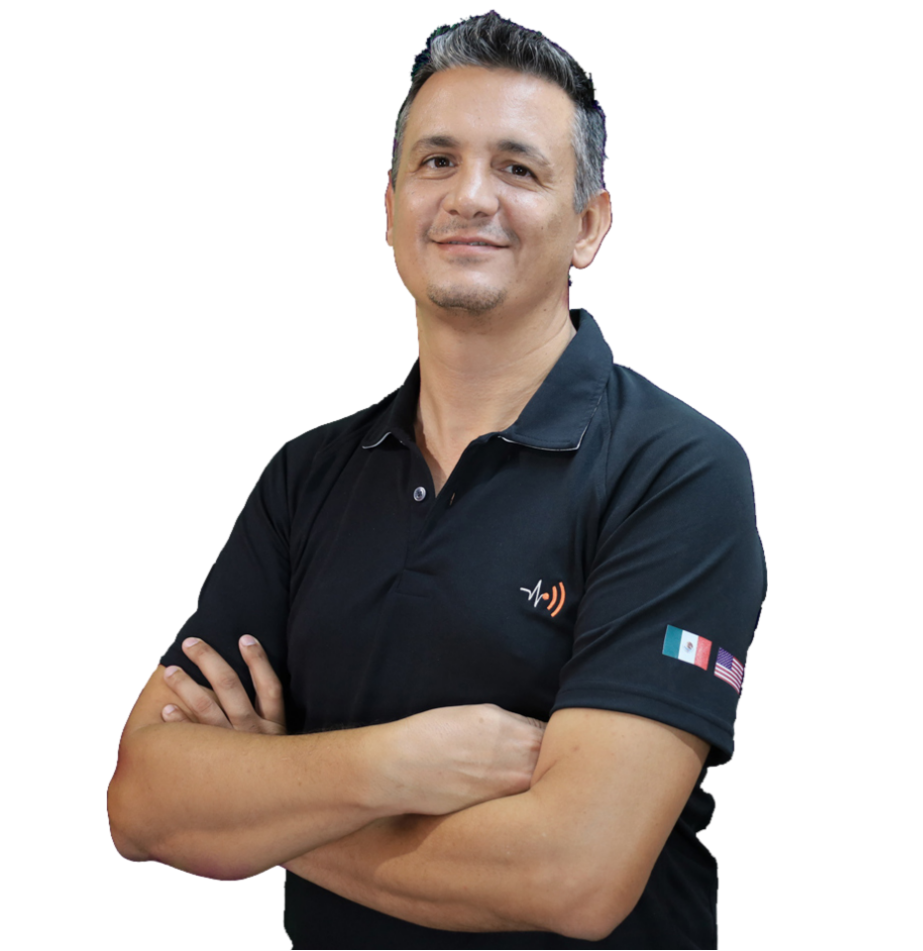
EI-WiSER
Full Bandwidth 15kHz
Ultra low-noise accelerometer
Long Distance Range up to 15m
IP67 Protection Grade
Li-ion Rechargeable Battery
Ideal for Route Based data Collection
DigivibeMX® M30
All the tools from DigivibeMX M20 and M10 in the same place
Wired or Wireless, your choice
Use it on up to 3 different computers
Machine Learning models for a batter analysis
ODS analysis
On and Off route recording
WiSER 3x
Full bandwidth 15kHz
Sensitivity of 100 mV/G
Long Distance Range up to 20m
Stainless stell housing
Operation temperature up to 185°F (80°C)
Ideal for Real Life ODS & Route based Recording