Simple Solutions for Complex Problems
Multiple Components, Multiple Forcing Functions, No Problem!
A large mobile equipment manufacturer was attempting to diagnose premature failures associated with this turbo charger system responsible for the main drive of the mobile equipment.
As with all mobile equipment there is a delicate balance between mass/weight and performance. As such, the manufacturer did not want to permanently instrument the system nor was it feasible to hardwire or use any kind of wireless sensor technology.
Video deflection technology using DragonVision® was the selected troubleshooting tool and was able to identify a number of key failure modes for correction.
Non-Contact Vibration Analysis
Since non-contact/non-invasive analysis is the only suitable approach for this users application the end user found themselves with a major dilemma trying to drill down to the root cause of the premature failures their customers were experiencing with this particular piece of mobile equipment.
This particular device ramped up to a steady state speed of around 3000 RPM. Further to that the customer utilized their iPhone recording in slow motion mode at 240 frames per second for data capture.
The user recorded the video and then uploaded it into DragonVision® for analysis. Identifying targets and static zones was required in this case because of the multiple components of interest and each component representing a failure mode.
During the target selection process specific focus was applied to the areas where the user suspected the root cause of 3 different failure modes was occurring.
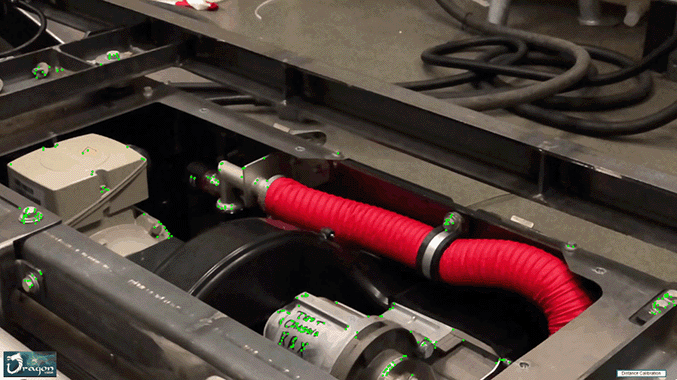
Accommodating for Transient Events and Processing the Video
Once the targets and static points were identified, it was important to consider the transient events that occur during startup and analyze the transient behavior without analyzing unnecessary idle data. To take into consideration the 3-4 seconds of transient startup the video analysis start and stop slide function was used to remove any non-applicable data.
The total processing time was around 35 seconds and total recording time was 2 minutes. At this point the end user has invested less than 3 minutes troubleshooting the problems with this assembly.
Phase Simulation Model
Once processing was completed a phase simulation model was performed and phase analysis clearly identified the problem. Despite precision alignment and manufacturing of the main drive pulley, it is found to be eccentric. Further, it was surprising to find that there was clearly enough misalignment that the combination of two faults resulted in a litany of different failure types.
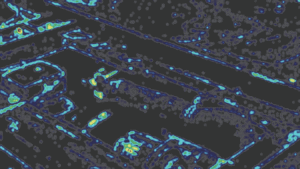
The above Vibrogram™ assisted the end user in identifying areas of maximum displacement as identified by DragonVision®. Identifying the dominant root cause via the myriad of tools available within DragonVision® make solving complex problems such as this an easy task. Creating visualized models such as phase, Vibrogram™, and video deflection gave the user the right set of tools to quickly, and easily identify the competing failure modes root causes.
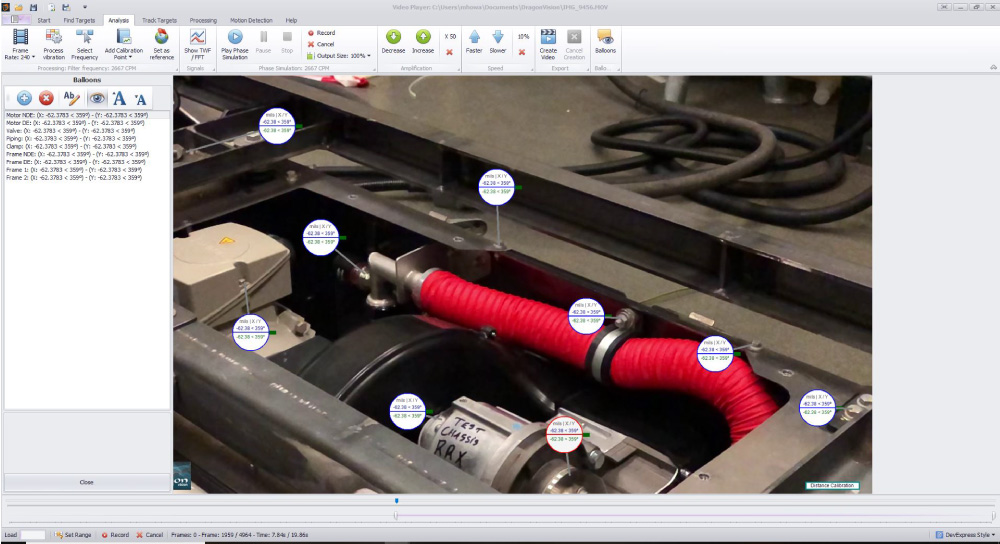
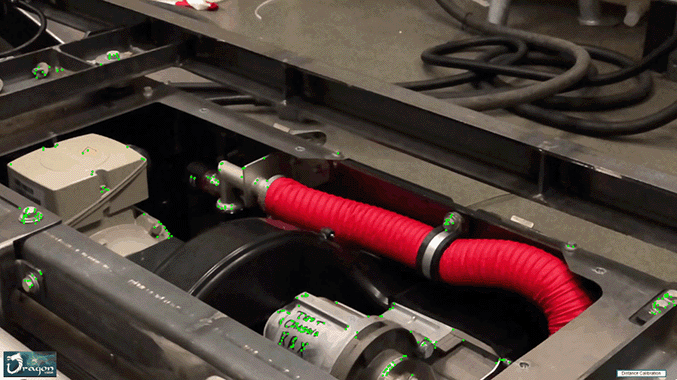
Completed Video Deflection Model
Another quick but efficient 5 minute analysis using DragonVision® video deflection technology helped the end user justify issuing a non-emergency recall that will ultimately lead to a higher level of reliability for the end users customers in the long run.
The DragonVision® video deflection model was used by the warranty resolution engineers to identify 2 failure modes and their appropriate corrective actions, while also releasing a recall that resolved the root causes for customers prior to the customer experiencing catastrophic failures with collateral damage.
In less than 10 minutes a problem that had been studied for nearly 130 man hours was solved using DragonVision® video deflection technology. Are you ready to see the unseen?

Dr. Michael Howard, is an American entrepreneur and Air Force veteran with a remarkable career in the predictive maintenance industry spanning over 30 years, and a variety of industrial sectors, including industrial manufacturing, reliability engineering, and instrumentation development and design organizations. Dr. Howard is a graduate of Excelsior University, Capella University, and New Charter University with degrees in Electro-Mechanical Engineering, Leadership and Organizational Management, and Engineering Management.
As the CEO of Erbessd Instruments, he leads strategy, sales, marketing, and operations in English-speaking markets. He is a certified reliability engineer, certified maintenance and reliability professional, and category III vibration analyst. Michael is a passionate advocate for wireless instrumentation, video deflection, and the Industrial Internet of Things (IIoT).
ERBESSD INSTRUMENTS® is a leading manufacturer of Vibration Analysis Equipment, Dynamic Balancing Machines, and Condition Monitoring with facilities in Mexico, the USA, the United Kingdom, and India.
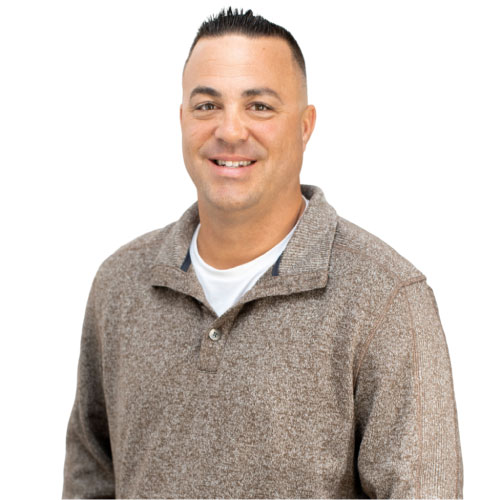