Torsional Vibration – New ways to measure it
Measuring torsional vibration has long been a formidable challenge for vibration analysts. However, a revolutionary breakthrough emerges with the advent of new wireless technologies. These cutting-edge advancements swing open the door to an uncharted world that was once shrouded in mystery. Journey with us as we witness the unveiling of an extraordinary application for these transformative technologies.
The introduction of wireless technologies revolutionizes the field of torsional vibration measurement, transcending the limitations of traditional methods. By harnessing wireless capabilities, analysts gain unprecedented ease and flexibility in capturing and analyzing torsional dynamics. This technological leap offers a gateway to previously unattainable insights, opening up vast possibilities for diagnostic techniques and maintenance strategies.
Don’t miss this momentous occasion as we showcase the potential of wireless technologies in reshaping the landscape of torsional vibration analysis. Join us on this captivating expedition as we explore the unbounded horizons it presents.
What is torsional vibration?
Torsional Vibration is defined as a sequence of slight changes in the rotation speed of an object. Similar to conventional vibration, torsional vibration is also defined by the amplitude and frequency of these changes.
Torsional vibration occurs when the rotating element is subjected to unequal loads during its operation. Common examples are reciprocating compressors and internal combustion engines. Since at one point in the cycle, the torque of one of the connecting rods is greater when air is compressed and decreases when air enters the chamber.
Because of this, the crankshaft reflects variations in the rotation speed that might lead to internal stresses, which in abnormal cases, can produce a rupture of the crankshaft (or shafts, depends on the machine).
Using wireless accelerometers to measure torsional vibration
This illuminating case study that explores the remarkable potential of employing Erbessd – Phantom wireless accelerometers for measuring torsional vibration. In this captivating analysis, we not only unveil the sensor’s technical data but also cater to the curiosity of those eager to delve deeper into this fascinating subject matter. Join us as we unlock a wealth of insights and equip you with the necessary knowledge to venture further into the realm of torsional vibration measurement. This comprehensive study promises to ignite your curiosity and provide invaluable information for those seeking to advance in this field.
How is torsional vibration measured?
One of the most common methods used for measuring torsional vibration is the calculation of the variation of the speed using an optical sensor and a piano-type tape. Hence recording the time difference between each step of the tape. There are certain restrictions for the measurement to be valid and reliable and one of them is the number of available samples per revolution since an incorrect sample rate can generate an aliasing effect or a saturation in the signal.
New Alternatives
The use of wireless vibration sensors in the industry can provide new ways to measure torsional vibrations. We can now measure torsional vibrations directly to the shafts with the same sampling rate and resolution capabilities of current vibration analysis. We can even permanently monitor the condition of a rotating element under regular operating conditions, to visualize the evolution of its torsional vibrations.
Case Study
We installed a high-range triaxial vibration sensor (PHANTOM EPH-V11E) at the crankshaft end of a 3.2 HP rated two-cylinder air compressor for torsional vibration study purposes. This study intends to prove that the sensor is able to send a readable signal while being attached to the rotating shaft and also to verify the presence that of a second harmonic, product of the sum of the vibration by the variation of torque and the vibration by the inertia of the crankshaft (known components of the vibration torsional in this type of machinery).
The nominal speed of spindle rotation is 900 RPM which is powered by a 3600 RPM single-phase electric motor using a 4: 1 ratio pulley.
Phantom EPH-V22 Wireless Accelerometer Features
- Frequency Range: 0 – 10 kHz
- Amplitude range: 32 g peak-peak
- Resolution lines: 6400
- Axes: 3
- Transmission type: Bluetooth
- Battery life: 3 years
Adventages
One of the notable advantages of utilizing PHANTOM for this study lies in the eccentric placement of one of its sensors, enabling the measurement of tangential vibration on the shaft (Figure 1). To evaluate the potential impact of mass variation within the system on compressor vibration, measurements were conducted both before and after attaching the sensor to the compressor shaft. The findings revealed a marginal 4% increase in the fundamental vibration (Figures 2 and 3), which, in the context of this study, was deemed negligible.
This observation suggests that the slight alteration in mass had minimal influence on the overall vibration characteristics of the compressor. These results underscore the robustness and reliability of PHANTOM in accurately assessing torsional vibrations in real-world applications.
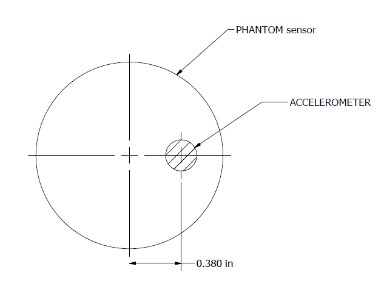
Figure 1 – Accelerometer’s eccentricity
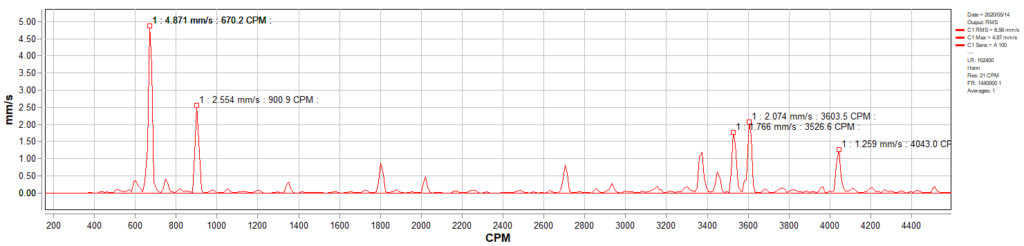
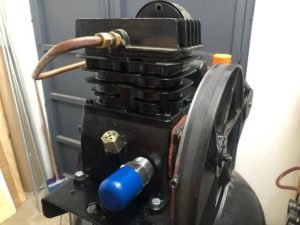
Figure 2 – FFT without Phantom
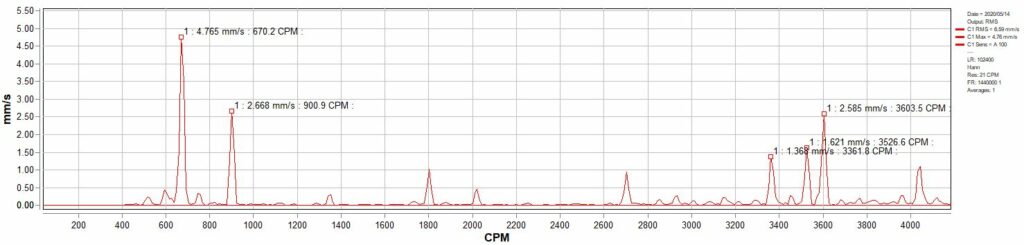
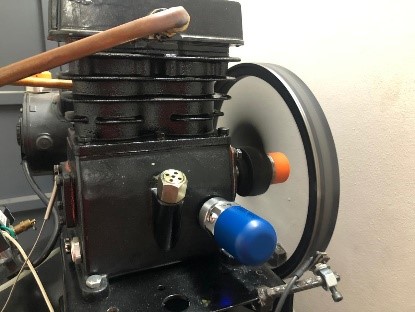
Figure 3 – FFT with Phantom
Recording data
I am happy to share with you the simplicity of sensor placement, the only thing I had to do is to screw the sensor axially to the shaft.
On the other hand, data recordings did not have any loss of data, nor corrupt signals. Additionally, we analyze the X-axis of the accelerometer, which is precisely the one that is tangential to the axis at a radius of 9.6 mm (0.380”).
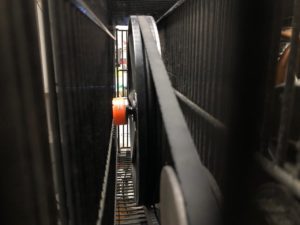
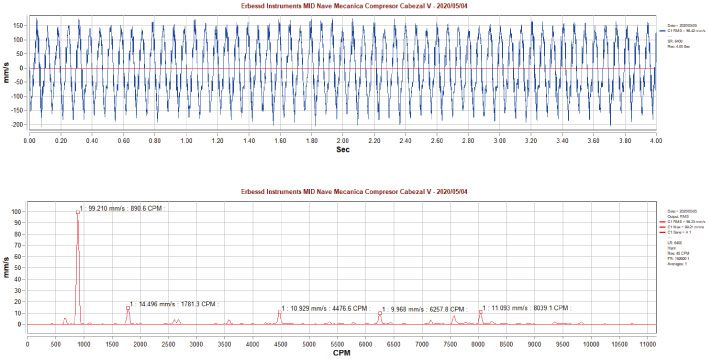
Figure 4 – Waveform and FFT of Torsional Vibration
I am convinced that what I got was the torsional vibration of the compressor, I am sure as well that this tool will be highly valued by analysts in this field. The spectrum shows second harmonics like those described in theory and even more.
Torsional vibration condition monitoring
We will leave the Phantom EPH-V11 sensor permanently mounted on the compressor to monitor its trend and spectra over time. Additionally, since the machine operation is intermittent, we linked PHANTOM vibration sensor to a Phantom EPH-S40 Hall Effect RPM measurement sensor. This way, the vibration sensor will only send meaningful data when the compressor is in operation.
Armando Torres, is a distinguished mechanical engineer, graduate of Autonomous Metropolitan University, and has more than a decade of industrial manufacturing, maintenance, and leadership experience. Armando is currently the Chief Mechanical Engineer, responsible for design and production for the ERBESSD INSTRUMENTS mechanical manufacturing department, specialized in the design and construction of balancing machines. Armando is a key contributor in the development of advanced solutions, positioning ERBESSD INSTRUMENTS at the forefront of the industry. His commitment to excellence and deep technical knowledge mark him as a leader in mechanical engineering.
ERBESSD INSTRUMENTS® is a leading manufacturer of Vibration Analysis Equipment, Dynamic Balancing Machines, and Condition Monitoring with facilities in Mexico, the USA, England, and India.
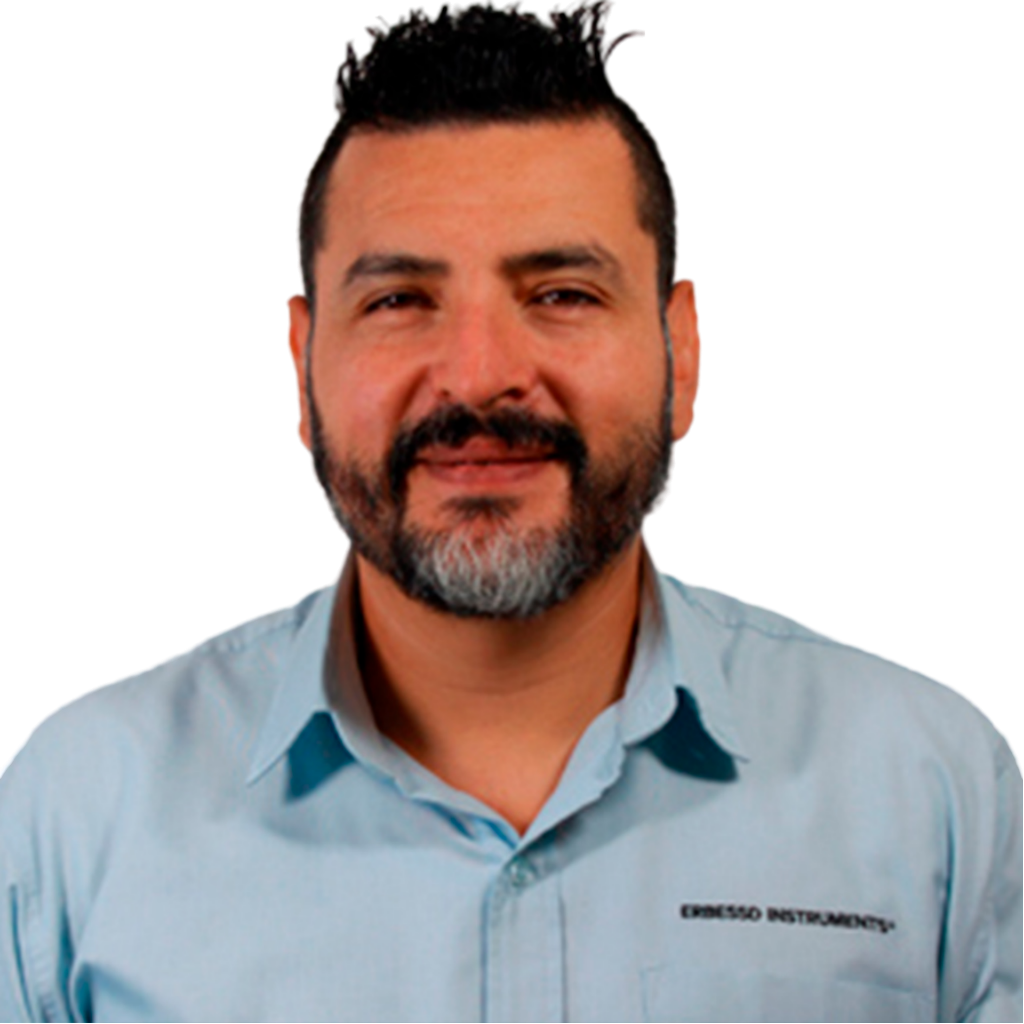