The 7 Most Important aspects about Condition, System & Equipment Monitoring
Technology in predictive maintenance is growing fast, and so are Condition Monitoring Solutions, which is one of its most important activities. In particular, the wireless sensors in Condition Monitoring Analysis changed completely the way we approach machinery reliability.
What is Condition Monitoring? What do we need to learn about modern technologies applied in it? Well, I am a Vibration Analysis technology developer, and I invite you to take some time to read these few tips I have written down for you.
What is Condition Monitoring in Vibration Analysis?
Condition monitoring is the process of periodically measuring one or more parameters in machinery to identify significant changes that usually indicate failures in the process or variations in vibration monitoring. It is an essential part of predictive maintenance that allows to plan maintenance actions focused on avoiding failures and their consequences.
For this reason, the condition monitoring process provides enough information to implement pertinent actions upon components that require them.
Condition vibration monitoring is usually applied to rotating machinery such as fans, compressors, pumps, combustion engines, and others.
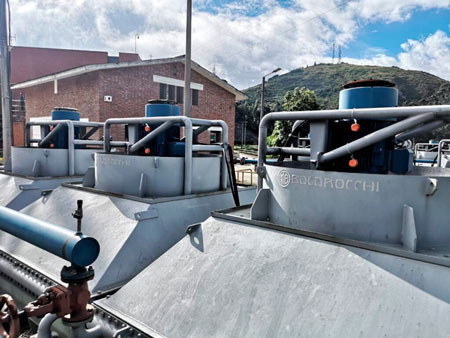
In Erbessd Instruments we created enough options of condition monitoring systems for you. From low-cost high-capacity equipment, to integral systems with multiple automatic parameters, such as our Phantom® Vibration and Condition Monitoring System.
Wireless Speed Sensor
EPH-S40 | Erbessd RPM Hall effect Sensor-
-
Switching Speed up to 600,000 RPM
-
Speed + Vibration sensor integration
-
Standby mode and long battery life
-
Configurable Measurement Interval
-
Configurable Alarm value
-
2 Replaceable LiON AAA bateries
-
IP67 Protection
Wireless Current Sensor
EPH-C31 | Erbessd 4-Phase Current Sensor-
-
Measures 4-Phase current simultaneously
-
Sends every 5min the max. value of a 15s reading
-
Compatible AC Split-core Clamps (50A, 100A, 250A, 500A)
-
Configurable Alarm value
-
Standby mode and long battery life
-
2 Replaceable LiON AAA bateries
-
IP67 Protection
Wireless 4-20mA Sensor
EPH-G61 | Erbessd General Purpose 4-20mA sensor-
-
Measures 4 Channels simultaneously
-
Compatible with any 4-20mA sensor output
-
Very Easy to install
-
Configurable Alarm value
-
Standby mode and long battery life
-
IP67 protection
Wireless Temperature Sensor
EPH-T20 | Erbessd Infrarred Sensor-
-
Measures temperature for object and ambient
-
Measure Range from -70 to +380°C
-
Configurable Alarm value
-
Standby mode and long battery life
-
Configure your sensor using your mobile
-
IP67 Protection
Wireless Temperature Sensor
EPH-T25 | Erbessd Thermocouple sensor-
-
Range of -210° to 1800° C
-
Measures temperature for object and ambient
-
Connect any type of Thermocouple
-
Configurable Alarm value
-
Standby mode and long battery life
-
IP67 Protection
-
2 Replaceable LiON AAA bateries
Analyze machinery performance
You can get tendency graphs of vibration monitoring, current consumption, changes in temperature, and pressure from your machinery. This way, you will know what the behavior trend is for each period. On top of that, you will be able to prioritize the order of condition maintenance. As a result, you will also be able to reduce downtime, and make better decisions about production plans as a benefit of predictive condition maintenance.
Reduce Maintenance cost with a Machine Condition Monitoring System
Some parts, such as gearboxes or bearings can be very expensive to replace, which is why a correct condition monitoring can increase components life span. Remember, condition monitoring is an investment that can pay off in the short term. The Wireless Condition Monitoring Sensor can be an indirect cost reducer.
Increasing production capacity with a condition monitoring system
Maximize your production capacity and make sure you work with reliable operation machines with our condition monitoring system. Design maintenance schedules accurately and create more efficient production plans to guarantee you meet delivery times and keep your customers satisfied.
Monitoring anywhere your are with our wireless condition monitoring system
This system allows you to be away from the company. Some Condition Monitoring systems are as easy as plug & play. Simply put, wireless sensors measure the condition indicator and transmit it to your own database. Now it is possible to have apps and web sites to display monitoring results, not only of a period of time but in real time as well. This can be done from a mobile device, tablet or computer anywhere you are with our online condition monitoring system.
There are a great number of techniques used in condition monitoring. Listed in here we have the most relevant ones:
- Vibration analysis
- Temperature monitoring
- Current measurement and analysis
- Speed Measurement
- Thermography
- Ultrasound
- Lubricant analysis
- Acoustic analysis
The criticality index of a system is often used to determine the type of condition monitoring solution that needs to be applied to your equipment. This index depends on the following factors:
- Economic impact due to an unexpected stoppage
- Cost of repair
- Environmental impact due to a stoppage
- Impact on security for staff
- Among others
Criticality index, therefore, divide the machines into 3 categories:
- Critical machinery: This type of machinery has the highest hierarchical level within the productive chain. It includes equipment such as power plants and steam turbines that are at the core of the operation. This machinery is vital, and as such, requires a very tight condition monitoring system. These machines are usually monitored by Phantom condition monitoring® system.
- Essential Machinery: These machines are an integral part of the production chain, however, in case of an unexpected failure, production will not be affected. Due to their more accessible cost, companies might have replacement systems placed in parallel to avoid production downtimes in case of failure. As the process continues, monitoring the condition of these machines is vital to implement alternative plans at the right moment. Because of this, permanent monitoring systems are the most commonly used in this type of machines as well.
- Non-critical machinery: These systems have a minor impact on production and do not usually represent an economic risk for the production chain. Condition monitoring of these machines is considered of low criticality, and a portable system is undoubtedly a good solution.
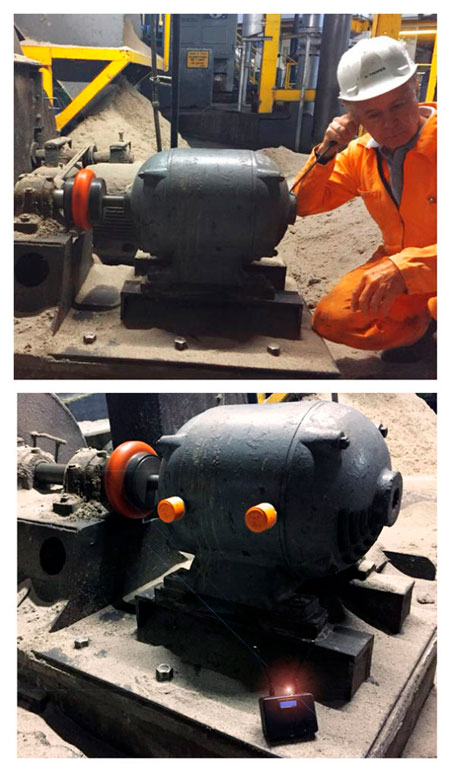
Economic aspects of Condition Monitoring Solutions
Savings due to production downtime reduction: The most significant savings arising from predictive maintenance are due to the significant reduction in production downtime.
The savings arising from downtime reduction can be calculated through the number of hours of downtime multiplied by the added value per hour for the process.
Cost of downtime = Downtime X $ Value per hour of process
Savings in maintenance costs: Additionally, Savings in maintenance are due to the reduction in man-hours to carry out repairs + savings due to the reduction of unnecessary replacements. This is calculated as follows
$ Savings in Hours = (Man Hours invested in Major Maintenance – Man Hours for minor maintenance) X $ weighted Hour / Man
Condition Monitoring Costs: The costs of condition monitoring systems depend on the chosen system which can be Permanent or Portable. Of course, Permanent systems require more investment if the number of machines is large. On the contrary, Portable systems are cheaper, although, they require a specialist to measure each machine periodically.
The main goal of machinery condition monitoring is to reduce its wear and tear by extending the lifetime of all its components. Either through the reduction of vibration or by improving its temperature conditions, the machine will have a lighter workload and several other benefits.
Electric power consumption: Making a mathematical correlation between vibration and energy is very difficult. Even more so because of the wide variety of machines that exist in a company. However, a study conducted by The Journal of Industrial Technology* proved that any given machine can consume twice as much current as it should only as a result of its vibration. Of course, this study was done in motors that can increase their vibration in such proportions that a big machine cannot replicate; nevertheless, the study does prove a realistic relationship between power consumption and vibration.
Safety and health: The reduction of vibration is closely related to the reduction of noise from a machine and, therefore, reduces the impact on the health of the staff in charge. Prevalence of conditions such as retinal detachment and hearing loss induced by noise can be reduced by applying a correct condition monitoring.
Environmental and Economic Impact. The ecological footprint left by corrective maintenance is considerably greater than that of preventive maintenance, because in the first one, the idea is to replace critical parts as well as lubricating them whether it is needed or not. These actions are intended to avoid stoppages, although they are not always necessary.
Implementing good preventive maintenance actions will not only reduce the environmental impact by avoiding all this waste, but will also have a much lower production cost.
*The Journal of Industrial Technology Vol. 13, No. 3 September – December 2017
Wireless Universal Sensor
EPH-MT | Erbessd Vibration, Current and Temperature-
-
10kHz FMax
-
Full waveform and spectrum data
-
Resolution Lines: 6400
-
Measures 3-Phase curent simultaneusly
-
Compatible AC Split-core Clamps (50A, 100A, 250A, 500A)v
-
2 Temperatures Channels
-
Range of -210°C to 1800°C
-
Connect any type of Thermocouple
Vibration and condition monitoring process has key aspects to achieve its goals in a short period of time. Nobody knows everything at the beginning of a process, so it is important consider the following advices:
You need to know what you want to measure: It is very important to decide what parameters you want to measure in a machine, as well as what machines you want to monitor. The most important parameters for condition monitoring are vibration, temperature and current.
Establish a starting point: You are probably not an expert analyst, and you don’t need to be either. The first step is to establish a starting point. As far as you are concerned, your machine is working fine right now, so you want to know if that changes. Setting a starting point will let you know when your machine exceeds current values. Over time, through valuable information and experience, you will know each machine’s real limits.
Periodic verification: None of this will work by itself, unless you make checking the status of your machinery and alarms a routine. Erbessd Instruments developed mobile applications, as well as PC and WEB software for you to have a simple way to do it.
- Condition monitoring application for IOS: Wiser Vibe
- Desktop application: Digivibe MX
- Website for condition monitoring: EIAnalytic.com
Set Alarms: At some point you will see that vibration or any other parameter changes. Verify your trend graph, evaluate and adjust your alarm values to know how soon they will be exceeded again.
Mobile Condition Monitoring App – WiSER VIBE
Wiser Vibe application is a 100% dedicated application for condition monitoring. Additionally, Wiser Vibe is also a data collector. It can work with our Wireless accelerometers or any of our Digivibe GX400 interfaces.
Share Wiser Vibe with customers or colleagues. Wiser Vibe is Free. This way your customers or colleagues can use it as well at no additional cost (not software cost). Hence, our app will update all end users on the latest events in the database, such as new information uploaded, or high vibration alarms as a part of our measure solution.
Route data collector: Wiser Vibe is also a route data collector. You can use Wiser Vibe for collecting data, as well as for balancing with any of our wireless accelerometers or Digivibe GX400 interfaces. Additionally, it is 100% compatible with Erbessd Phantom condition monitoring.
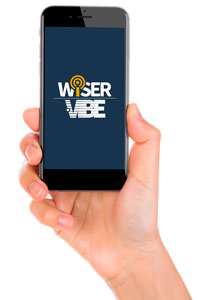
Receive Notifications of Alarms: Wiser Vibe warns you 24 hours a day on any abnormal event of the machinery when you use Phantom condition monitoring. In case it is necessary, you can readjust these alarms at any time according to the needs of each machine.
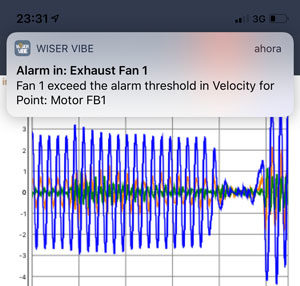
Off-Route analysis: You can do off-route analysis with Wiser Vibe. Save the signals, send them by email, share them with Digivibe or in the cloud.
Scan the code of your machinery: Are you walking through your company and you are curious about the current condition of a machine?
Take your phone and Scan the QR code. Wiser Vibe will give you the latest recorded vibration values, alarms, and spectrum with a single click.
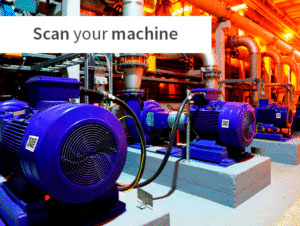
Dr. Thierry Erbessd, a prominent Mexican entrepreneur, and graduate of the National Polytechnic Institute has revolutionized the field of Vibration Analysis, Dynamic Balancing, and Condition Monitoring. Through his innovative software DigivibeMX®, DragonVision®, and WiSER Vibe®, he has set a before and after in the industry. As president of Erbessd Instruments®, he has not only led the company to the top of the global industrial maintenance industry but has also expanded its influence with strategically located offices in America, Europe, and Asia, establishing himself as an undisputed reference in industrial maintenance solutions worldwide.
ERBESSD INSTRUMENTS® is a leading manufacturer of Vibration Analysis Equipment, Dynamic Balancing Machines, and Condition Monitoring with facilities in Mexico, the USA, England, and India
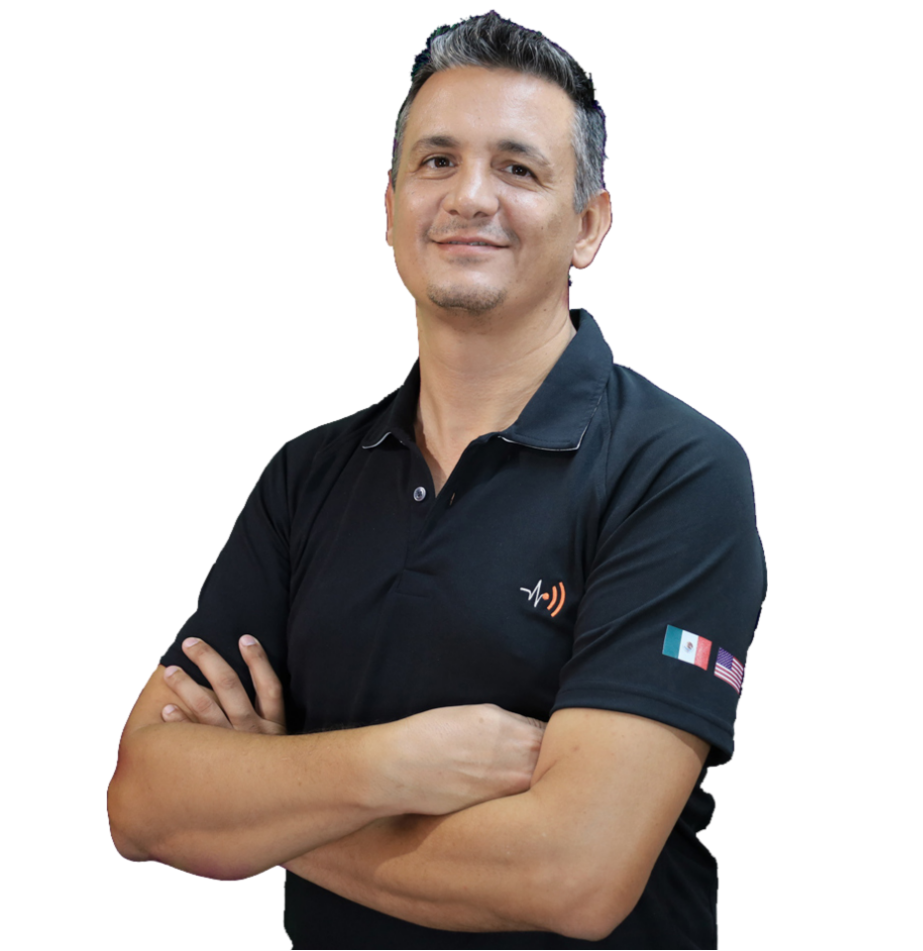