Case Study: Advantages Of Using Band Filters with Acceleration Envelope
Findings
Can #13 Drive Side bearing’s readings indicate an inside race fault-cracked (suspect it has gone up the taper).
Dryer Can Speed = 123 rpm.
Recommmmendation: Suggest changing bearing out before shaft or housing damage occurs.
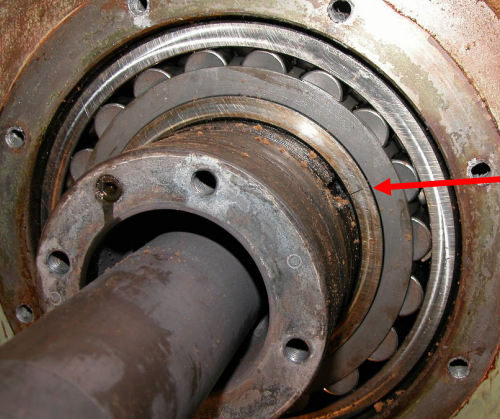
Amplitude will not necessary change or determine the severity of the fault with heavy mass equipment. Frequency content is crucial for slow speed analysis
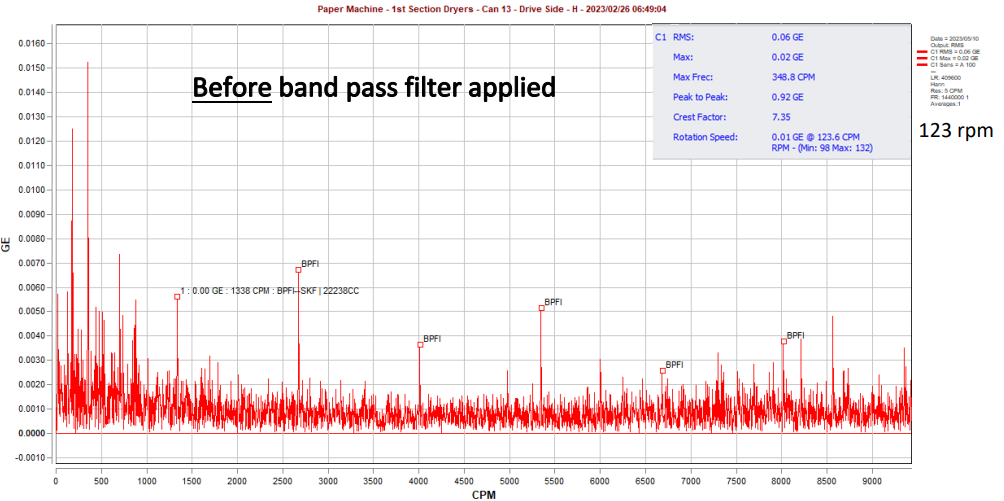
Apply a band filter at the frequency range that the bearing rings to emphasize the bearing fault
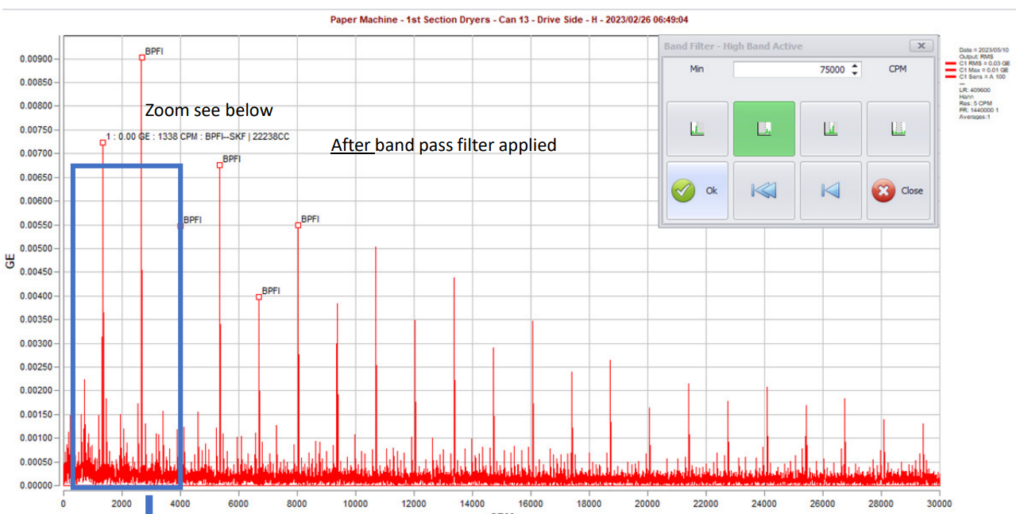
When the High Pass Band Filter is applied the Inside race fault is seen clearly with the running speed sidebands
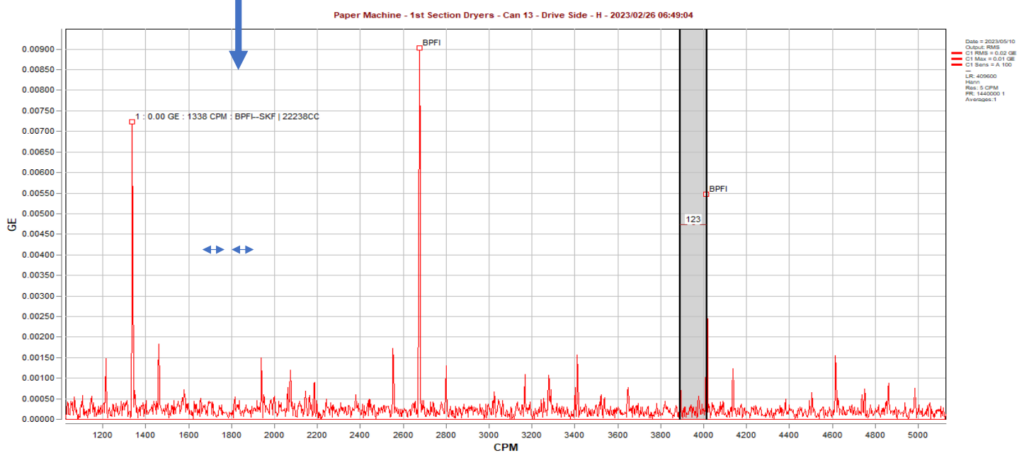
On equipment that you are not familiar with, you should experiment with several filters because you do not always know where the bearing ring thanks to ERBESSDÂ
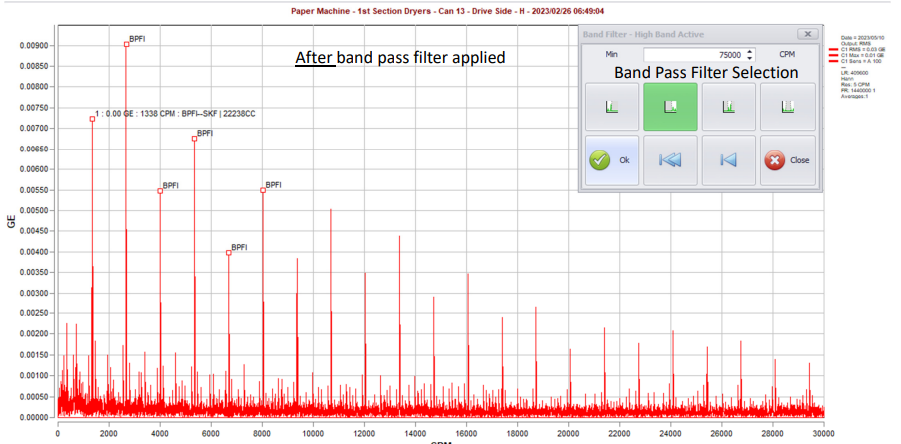
Digivibe software is capable of applying different band filters, a useful tool for an analyst
Paper Mill planned to have the bearing replaced before further damage occurs
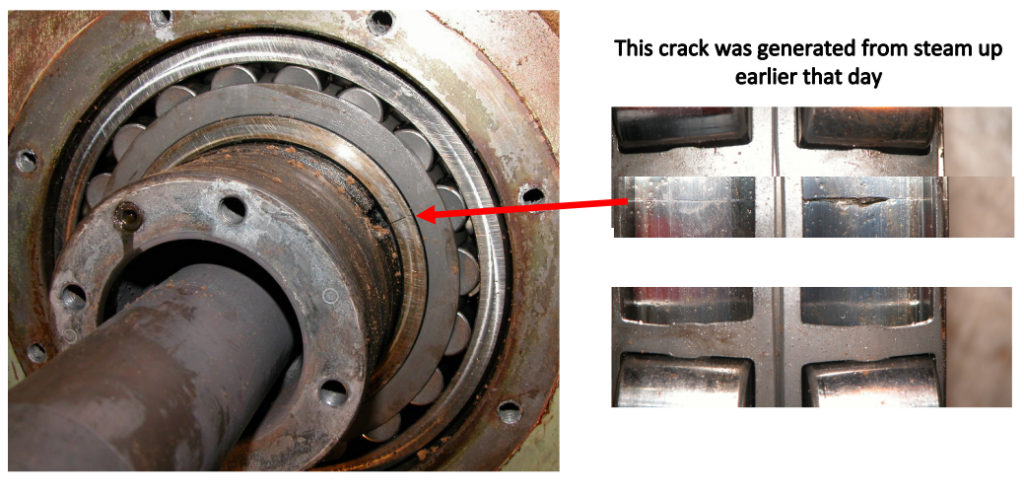
Common issues
Avoidance: Potential catastrophic failure, shaft and/or housing damage
Example of when a taper bore bearing cracks, one set roller end up taking the load Similar bearing failure that ran for 1 week after the inside race crack was diagnosed A cracked bearing can produce catastrophic failure in the shortest time period than any other bearing failure,
except maybe cage failure
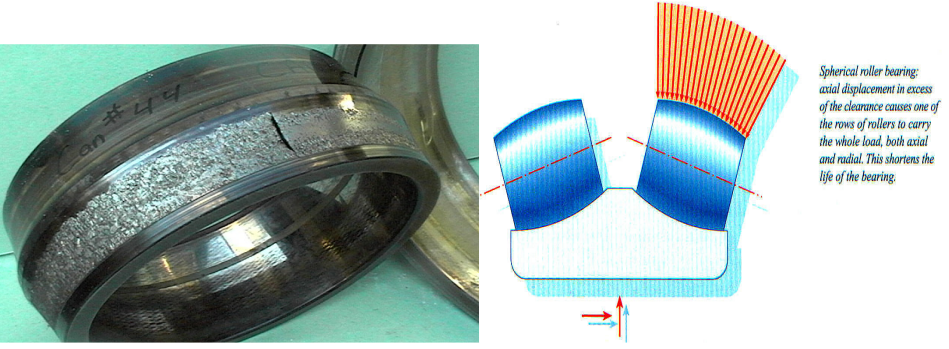
Michelle Charlebois,
Vibration Analyst / Manager of Vibration Integrated Technology Services Ltd. (V.I.T.S. Ltd). Currently working in Ontario, Canada with 12 years in the Predictive Maintenance field. Michelle is a graduate in Instrumentation and Control, Category 2 Vibration Analyst and Level 1 Ultrasound Certified.
Proud user and Distributor of ERBESSD INSTRUMENTS® Products. Utilizing Online Condition Monitoring Systems and route data collection providing timely analysis and recommendations, improving machine availability in today’s competitive industrial environment.
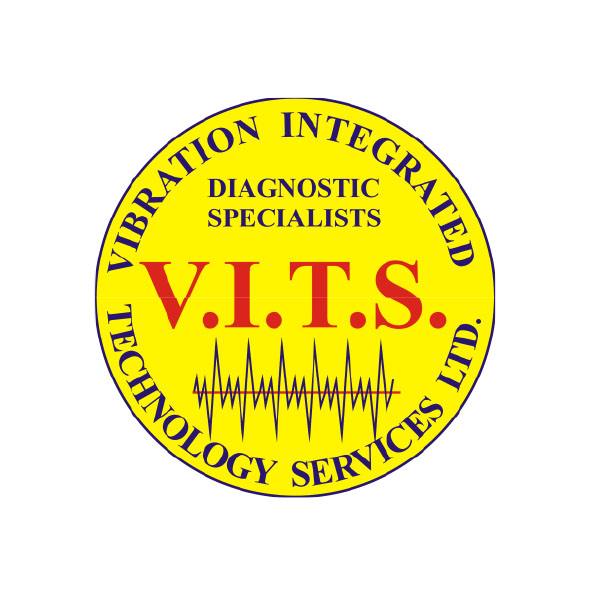